Wednesday, February 28
FPGA Calculator Uses Joystick
FPGAs are great fun, but sometimes you need a few starter projects under your belt. These projects might be something you could just as well do with a CPU, but you have to start somewhere. [LambdaPI] recently shared a 4-bit calculator created using an FPGA, and you can see it in the video below.
The calculator uses a Papilio FPGA board and a LogicStart accessory board for the display and switches. The Papilio normally uses schematic-based entry and Arduino code, but [LambdaPI] used VHDL. You enter the two 4-bit numbers on the 8 switches and then the joystick selects one of four operations (add, subtract, multiply, and divide).
Inside the code, you’ll see that the FPGA does all four calculations at once. The joystick just selects which outputs go to the display. Each module also decodes the LEDs separately which is an interesting design choice. On the negative side, it duplicates a lot of code, but there is no need to change the format with for example division (which shows as a fixed-point decimal number).
We’ve seen Papilio boards doing duty as a 128 MHz Z80 CPU. Or you can use one to create an Ambilight. However, as a first project, this calculator can really fit the bill. If you don’t have any hardware, you could experiment with using EDA Playground.
Disney’s Wreck-It Ralph 2 plans to “break the Internet” this Thanksgiving
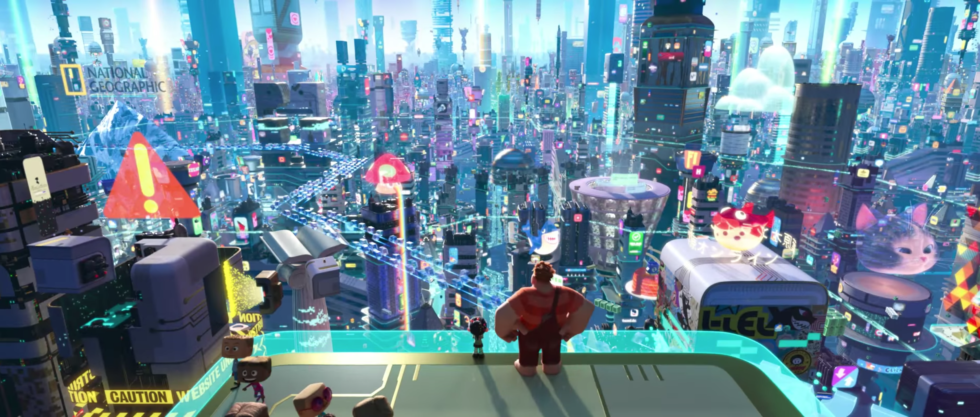
After sending up various eras of video games in 2012, Disney's Wreck-It Ralph film series will return to theaters with a sequel this Thanksgiving—and Wednesday's trailer sees the franchise changing its jokes and references to an Internet theme.
Disney isn't being shy about the sequel's title, opting for the ambitious-sounding Ralph Breaks The Internet: Wreck It Ralph 2. However, the trailer doesn't show the titular hero, voiced again by John C. Reilly, facing off against Kim Kardashian's butt. Instead, the two-minute trailer shows him and his cohort Vanellope (again voiced by Sarah Silverman) shooting through a series of tubes to land in an avatar-filled approximation of the Internet.
Repairs You Can Print Contest: Meet the Winners
Six weeks ago, we asked you to show us your best 3D printed repairs for a chance to win $100 in Tindie credit and other prizes. You answered the call with fixes for everything from the stuff everyone has, like zippers and remotes, to the more obscure stuff, like amazing microscopes scavenged from dumpsters.
It was hard to whittle down the entries we received into the top 20 because you came up with so many awesome fixes. A few of them had us thinking hard about the definition of repair, but are brilliant in their own way.
So without further ado, we are pleased to announce the winners of our Repairs You Can Print contest. We also want to give honorable mention to those projects that wowed us with ingenuity.
The Top Three Winning Entries
Here are the highest-ranked entries chosen from the twenty winners. Each of these repair projects came with considerable design hurdles, but each of their engineers persevered and came out smelling like a rose (made of melted plastic, of course).
First Place: Fixing a Chewed-Up Remote
When [Alex Rich]’s dog chewed up his $90 home theater remote a few years back, he saw an opportunity to more than just replace the case. Any time the furnace or A/C kicks on in his house, it’s just noisy enough to warrant turning up the volume a little bit. Of course, once it shuts back off, then the volume is too loud.
[Alex] had just enough leeway in the new design—and space inside the case—to add a Trinket that communicates with his thermostat and adjusts the volume accordingly. He also hid a hardware power switch on the underside of the remote to prolong battery life. Not only does he have an improved and working remote, he has an interesting conversation piece for the coffee table.
Second Place: Replacement Drill Battery Pack
Sometimes it seems that planned obsolescence knows no boundaries. Manufactures will move on to the next design or the newest battery composition without a second thought, except the one where they get to force their way back into consumers’ wallets.
[Larry G] wasn’t going to play that game when it came to his old Ryobi drill. He figured that as long as he could approximate the shape of the old pack and get the connections right, he could replace the NiCad pack with commonly-available rechargeable Ni-MH cells. The new pack is wired such that it only supports the max speed, but [Larry] may revisit the project and try to add PWM speed control with a 555.
Third Place: Microscope Mounting Bracket Repair
What’s the best thing you ever found while dumpster diving? [leumasyerrp] snagged a $1500 Vision Engineering Mantis Microscope that had been thrown out, presumably because the mounting bracket splintered into pieces and made it unusable.
He printed a new bracket in PLA and attached it with bolts and nylon lock nuts. So far, it holds up the heavy microscope really well. The tricky part was trying fasten it so that the microscope has enough play to pivot, but not so much that it droops after being positioned.
20 Winners of $100 Tindie Credit
This is the complete list of 20 hackers who have been awarded $100 in Tindie credit in recognition of their awesome efforts to fix their stuff. You can browse all the contest entries here.
- 3D Printed Zipper Box
- 3D printed belt for Phillips CD-i
- 3D printed universal cable fix
- Barrel Chair Bearing Repair
- Chewed up remote repair
- Corvair replacement parts
- Customizable Portaholder for Baratza Vario
- Hololens Headband Repair Kit
- MANTIS MICROSCOPE REPAIR
- NLA: DeWalt DW708 Mitre Saw “Dust Extactor”
- Nexus 7 2013 Sim Card Tray
- Ninja Blender Black to Gray Adapter
- PRSOUC35K glue gun revival (3D printed part)
- Printing Molds for Rubber Repairs
- Repairing a tool wall organiser
- Repairing my toolbox with a 3D printed part
- Replacement Battery for Ryobi 7.2v Drill
- Replacing a Disintegrated Rinse Aid Dispenser Lid
- Solder Sucker Repair
- Trigger Keys for MSX Computer
The Special Prize Winners
And now, the moment you’ve all been waiting for.
At the start of this contest, we offered a special prize to the best student-made repair and another to the best fix from an organization. These two winners have each been awarded a Prusa i3 Mk3 with the multi-material upgrade, which lets it print with up to four colors or materials at once without manual reloading.
Best Student Entry: Barrel Chair Bearing Repair
Our best student entry used the power of extruded plastic to re-invent the bearing and save a swiveling barrel chair.
Years ago, [Matt]’s parents found a comfy swiveling chair that didn’t turn anymore. Since the bearing was riveted shut, he couldn’t just clean out the crud and repack it. He had to rebuild it.
If you’ve never played with a printed ball bearing, they’re usually rough enough to be non-functional. [Matt] designed around the constraints of printing and came up with what we can only describe as a flat tapered roller bearing.
The rollers are tapered cones designed to roll at the same rate at both ends. [Matt] made a 70mm-diameter proof of concept bearing first. It moved really well, so he scaled it up to fit the chair. The new bearing withstood weight just fine, but swiveling made the center post tear away from the bearing. He printed a replacement in TPU, and it’s been smooth swiveling ever since.
Best Organization Entry: 3D Printed Prius Hatch Release Switch Cover
Our best entry from an organization used some fused deposition modeling to re-engineer a mistake that’s baked into the Toyota Prius.
[Mark] had a problem with his Prius. The hatch release mechanism has this soft rubber cover that gets gooey in the summer and becomes too stiff to work properly in the winter.
He asked his friends at Milwaukee Makerspace for help, and they designed a replacement cover, printed it in TPU, and sealed it with silicone to keep water out. It’s worked well for over a year and flexes in any weather, even below 0°F/-17°C.
The Honorable Mentions



We had many, many entries that weren’t actually repairs: nothing was broken before it was fixed. But some of these were so cool that we thought we’d give them a shout-out.
[Andrew] needed a variable-speed pump, but all he had lying around was a 3/4 HP fixed-speed pump from Harbor Freight. He bought a BLDC motor and Frankensteined it to the pump by printing an adapter flange, an axial fan to cool the new motor, and a housing to marry it to the pump. How does she chooch? 850 GPH at max speed!
[Ben]’s engineering teacher came to him with an interesting assignment: build a prosthetic for [Grey], a puppy born with a short leg that his teacher met at his own puppy’s obedience school. [Ben] came up with a 20-piece adjustable prosthetic that works with the puppy’s elbow joint. It’s 100% parametric, so [Grey] can scamper into adulthood on an even keel.
[Nelson] was tired of killing vacuum cleaners with filter-clogging fine particulates, so he designed and printed a 7-vortex cyclonic extractor to collect the particles before they can reach the filter. Thanks to the power of physics, he’s going to save about $100 a year and a whole lot of time.
Amazing Entries
A 3D printer is the ultimate design tool for one-off fabrication, and when it comes to repairing bits of broken plastic in our lives, there’s no better option than a 3D CNC hot glue gun.
It was exceptionally hard to decide on the winning entries for the Repairs You Can Print contest, and we wish we could award everyone a prize. The work that came out of the Hackaday community went above and beyond, and we were amazed by what we saw. Thank you to all that entered, and to anyone who chooses to repair their bits and bobs of consumer electronics instead of throwing them away.
War Stories: Brad Wardell remembers the mystery error that killed Elemental
Video shot and edited by Justin Wolfson. Click here for transcript.
Welcome back to "War Stories," our ongoing video series looking at game devs tackling complex programming challenges. Check out our previous chats with Looking Glass founder Paul Neurath and Ultima designer Richard Garriott.
Any fan of space-based turn-based strategy games should know the name Brad Wardell. For decades now, Wardell and his studio Stardock have been behind the well-loved Galactic Civilizations series, which started on the ill-fated OS/2 before finding success on Windows years later. The studio's space-RTS empire also includes Sins of a Solar Empire and Ashes of the Singularity, keeping alive a genre that has fallen into obscurity in recent years.
Around 2010, though, Wardell and Stardock took a turn away from sci-fi and towards high fantasy with the extremely ambitious Elemental: War of Magic. As Wardell recalls, the development plan called for units that could marry and have children that really aged, fully designable cities, and individual units that could each be fully outfitted with their own sets of clothes.
Friday Hack Chat: Everything PCB
It was not too long ago that all PCB design packages were proprietary. Getting PCBs made was expensive, and if you tried to do this over the Internet, the best way was to download a board house’s proprietary software, design your board in their software suite, and send your boards off to be made. A 5 cm square board would cost two hundred dollars. I know this to be true because I’ve said it before, and no one has corrected me.
For this week’s Hack Chat, we’re talking Everything PCB with OSH Park. OSH Park is the leading creators of perfect purple PCBs. They have POGs, and for the last two weeks, they’ve been one of the few places you can send some Gerbers to and have it manufactured in a timely manner if you live in the US. Because China was closed.
For this week’s Hack Chat, we’re going to be talking about everything PCB. How do you do castellated holes? How do you mill slots and square or otherwise non-round holes? Internal cutouts? Stop mask expansion? Artwork? Panelization? Why purple? More POGs!
Our guests for this chat will be [Dan Sheadel] and [Drew Fustini] of OSH Park, and they’re going to be there answering all your questions. [Dan] has been around OSH Park from the beginning and enjoys designing tiny useless robots and mentoring students building better ones. [Drew] is an Open Source hardware developer, firmware designer, a BeagleBoard board member, and is usually found at hardware meetups wearing purple.
Our Hack Chats are live community events on the Hackaday.io Hack Chat group messaging. This Hack Chat is going down Friday, March 2nd at noon, Pacific time. Want to know what time this is happening in your neck of the woods? Have a countdown timer!
Click that speech bubble to the right, and you’ll be taken directly to the Hack Chat group on Hackaday.io.
You don’t have to wait until Friday; join whenever you want and you can see what the community is talking about.
Detoured: Fabbing At The Art Institute Of Chicago
[Majenta Strongheart] is one of the talented folks who works at the SupplyFrame Design Lab, home to dozens of Hackaday meetups, the Hackaday Superconference, and when the shop floor isn’t filled with chairs, is the place where tons of awesome projects are fabricated. [Majenta]’s role at the Design Lab is a Staff Designer, where she’s responsible for working the machines, and holds the distinction of being in the room when the SawStop kicked for the first time. Don’t fret: it was mirrored acrylic.
Among [Majenta]’s other duties at the Design Lab is on the social media front, showing off the capabilities of other design spaces around the country. Her first video in this series is from her alma mater, the Art Institute of Chicago. In this video, [Majenta] takes a look at the incredible fabrication facilities found here.
The tour begins in an exceptionally well-equipped wood shop kitted out with panel saws, spindle sanders, bandsaws, and not enough clamps. From there, the tour moves over to the metal shop and — unique for the city of Chicago — a forge. A long time ago, after Philadelphia and New York were the tech centers of America, and before the Bay Area was the tech center of America, Chicago made everything. The forge at the Art Institute of Chicago is the last remaining place in the city where metal casting takes place. This space was grandfathered in, and still remains a place where students can cast objects out of bronze and aluminum.
The Art Institute of Chicago is a very, very well equipped space full of enough tools to make anything you want. If you’re looking for some inspiration on what your basement, garage, or local hackerspace should look like, you need only look at [Majenta]’s tour. You can check out the entire video below.
Porsche plans for Mission E electric car, will build fast-charger network
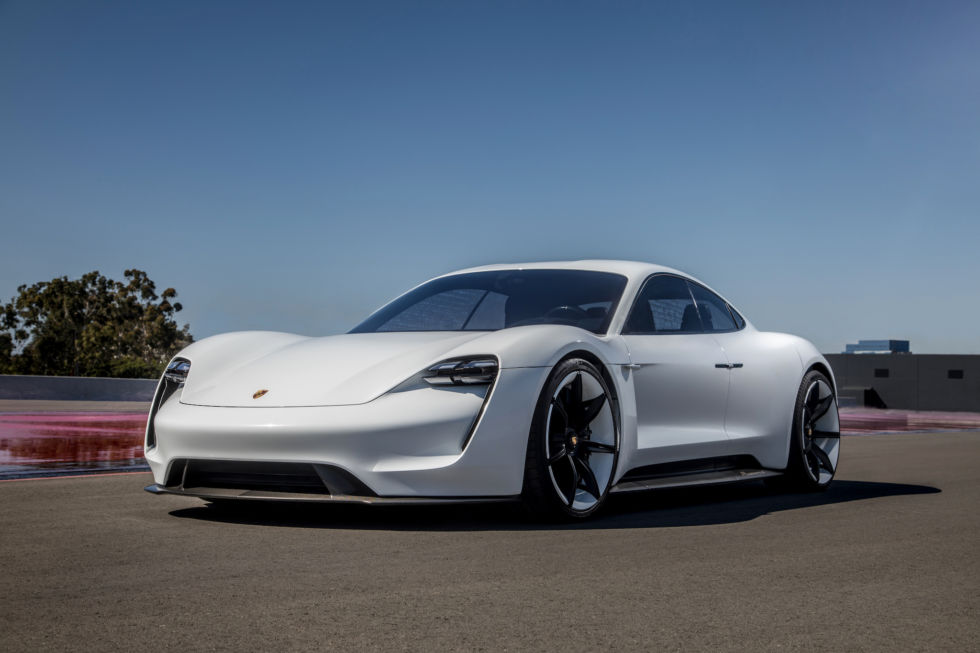
Porsche
The electric vehicle market is finally about to get interesting. It's been some time since Tesla proved that EVs didn't have to involve hair shirts, and at long last some other automakers are ready to enter the fray. Later this week at the Geneva Motor Show, Jaguar is going to reveal the I-Pace, which goes on sale shortly. Audi is readying its e-tron for later in the year. And Porsche has the Mission E.
The Mission E is a sleek four-door that promises 600hp (447kW) and 310 miles (500km) of range from a 95kWh battery pack. We first saw a concept of the Mission E back in 2015. Such was the reaction that Porsche had to green light the program.
Teardown Of An UWB Location Beacon
Outdoor navigation is a problem that can be considered solved for decades or maybe even centuries, depending on the levels of accuracy, speed and accessibility required. Indoor navigation and location, on the other hand, is a relatively new field and we are still figuring it out. Currently there are at least four competing technologies pushed by different manufacturers. One is ultra wide band radio and [Marco van Nieuwenhoven] shows us what a beacon using this technology is made of.
In his thorough tear down of an Estimote location beacon, he comes up with a complete parts list and schematics for each of the four PCB layers. The beacons are controlled by a Cortex M4 and feature Bluetooth radio in addition to the UWB part. They also come with a three-axis accelerometer, temperature, ambient light and pressure sensors and NFC capability. These boards combine a lot of functionality in a compact package and [Marco]’s stated intent is to create an open source firmware for them.
Hacking proprietary hardware, especially when doing so in public may get you in legal trouble, but in this case [Marco] has contacted the manufacturer, and the relationship seems to be friendly so far. Let’s hope it stays that way; these things look like a promising platform and may become a lower cost alternative to the evaluation kit running the same UWB radio we featured earlier. Alternatively you could ditch the UWB and use WiFi for indoor location.
The Faces of Maker Faire Kuwait
A sand sculpture of a mosque, a beach cleaning robot, an underwater robot for monitoring oil spills in the ocean, wooden models of the traditional sailing boat known as a dhow, a proof of concept for an air conditioner that uses ceramic tiles to reduce the amount of electricity used […]
The post The Faces of Maker Faire Kuwait appeared first on Make: DIY Projects and Ideas for Makers.
Cook Up Your Own High-Temperature Superconductors
It looks more like a charcoal briquette than anything, but the black brittle thing at the bottom of [Ben Krasnow]’s crucible is actually a superconducting ceramic that can levitate magnets when it’s sitting in liquid nitrogen. And with [Ben]’s help, you can make some too.
Superconductors that can work at the relatively high temperature of liquid nitrogen instead of ultracold liquid helium are pretty easy to come by commercially, so if you’re looking to just float a few magnets, it would be a lot easier to just hit eBay. But getting there is half the fun, and from the look of the energetic reaction in the video below, [Ben] had some fun with this. The superconductor in question here is a mix of yttrium, barium, and copper oxide that goes by the merciful acronym YBCO.
The easy way to make YBCO involves multiple rounds of pulverizing yttrium oxide, barium chloride, and copper oxide together and heating them in a furnace. That works, sort of, but [Ben] wanted more, so he performed a pyrophoric reaction instead. By boiling down an aqueous solution of the three components, a thick sludge results that eventually self-ignites in a spectacular way. The YBCO residue is cooked in a kiln with oxygen blowing over it, and the resulting puck has all the magical properties of superconductors. There’s a lot of detail in the video, and the experiments [Ben] does with his YBCO are pretty fascinating too.
Things are always interesting in [Ben Krasnow]’s life, and there seem to be few areas he’s not interested in. Of course we’ve seen his DIY CAT scanner, his ruby laser, and recently, his homemade photochromic glass.
Replicating an Ancient Pump Drill
Chris from Clickspring recreates the type of push drill that was likely used to fabricate the ancient Antikythera Mechanism .
The post Replicating an Ancient Pump Drill appeared first on Make: DIY Projects and Ideas for Makers.
Tuesday, February 27
King of the crossovers? The 2018 Volvo XC60 T8 makes a convincing case
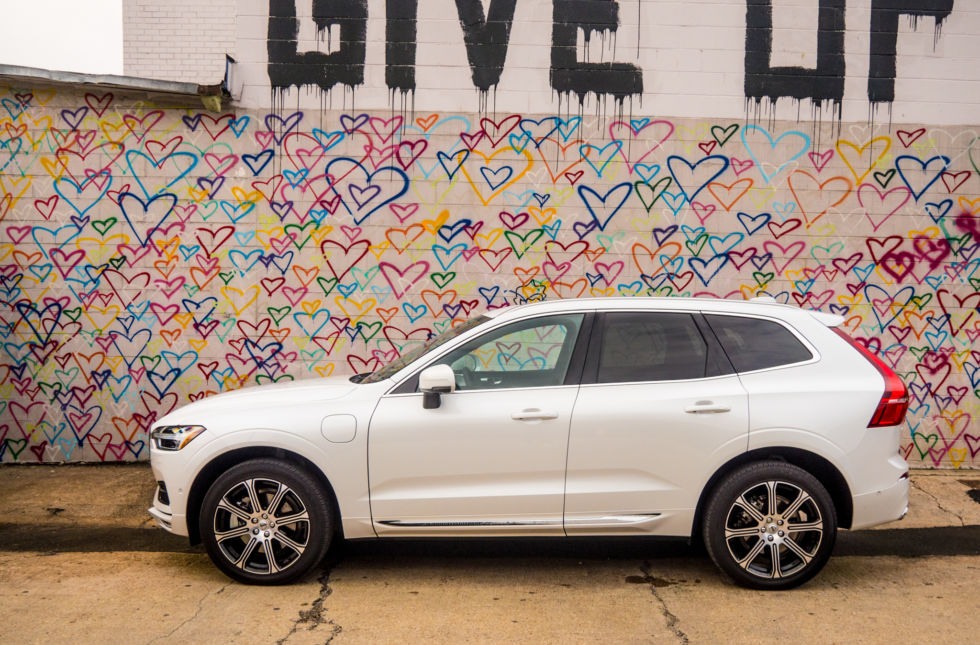
Jonathan Gitlin
The renaissance at Volvo is in full swing. Flush with funds and a supportive owner, its products over the past few years have proven you don't need to look to Germany to see a luxury car maker at the top of its game. This corner of the market is now all about the swanky SUV, and the 2018 XC60—tested here in its 400hp T8 plug-in hybrid version—makes a strong case that Sweden is leading the pack.
The new era started when Ford sold Volvo in 2010. Freed from American corporate micromanagement, new owner Geely took a hands-off approach, giving Volvo the resources it needed to develop all-new engines and vehicle architectures. It came up with what it calls the Scalable Product Architecture, a highly flexible starting base for all of its medium and large vehicles. The first SPA vehicles were all big ones: the XC90, a three-row SUV that arrived in 2014; then more recently the S90 sedan and V90 station wagons. All are fine vehicles, but with the XC60, the stakes are higher—it's far and away the company's best-selling model.
Definitive Dog Feeding with Arduino
Some dogs have no sense of self-preservation. Given the opportunity, they will eat until they’re sick. It’s up to us humans to both feed them and remember doing it so they aren’t accidentally overfed. In a busy household with young children, the tricky part is the remembering.
[Bryan]’s family feeds their dog Chloe once a day, in the mornings. She was a rescue who spent a few years scrounging for meals on the street, so some part of her is always interested in finding food, even if she just ate. Each morning, the flurry of activity throughout the house is compounded by Chloe’s repeated requests for food, so [Bryan] got his kids involved and built a simple circuit that lets everyone know—at a glance—whether Chloe was fed.
Chloe’s kibble is kept in a touch-top wastebasket that flips open at the press of a button. [Bryan]’s dog-fed detector uses a reed switch and an Arduino clone to detect when the lid is opened. When the reed switch goes, low, the Arduino lights up an LED. The light stays on for two hours and then shuts off automatically to get ready for the next day. You don’t have to beg for a demo video, because it’s waiting for you after the break.
Since Chloe devours a bowl of food in about two minutes flat, maybe the next project for [Bryan]’s family could teach her to slow down a bit.
In-the-wild DDoSes use new way to achieve unthinkable sizes
Hackers have found a way to amplify distributed denial-of-service attacks by an unprecedented 51,000 times their original strength in a development that whitehats say could lead to new record-setting assaults that take out websites and Internet infrastructure.
DDoS vandals have long intensified their attacks by sending a small number of specially designed data packets to publicly available services. The services then unwittingly respond by sending a much larger number of unwanted packets to a target. The best known vectors for these DDoS amplification attacks are poorly secured domain name system resolution servers, which magnify volumes by as much as 50 fold, and network time protocol, which increases volumes by about 58 times.
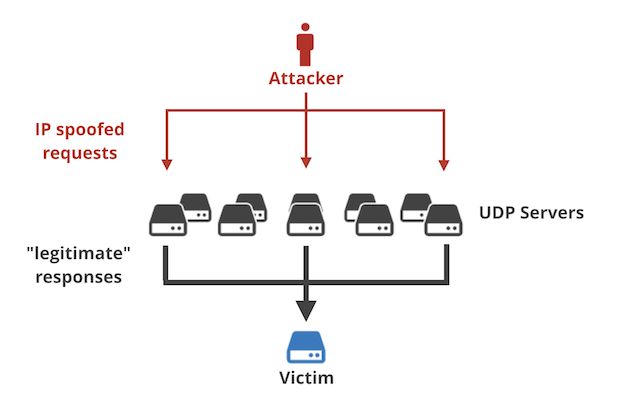
(credit: Cloudflare)
On Tuesday, researchers reported attackers are abusing a previously obscure method that delivers attacks 51,000 times their original size, making it by far the biggest amplification method ever used in the wild. The vector this time is memcached, a database caching system for speeding up websites and networks. Over the past week, attackers have started abusing it to deliver DDoSes with volumes of 500 gigabits per second and bigger, DDoS mitigation service Arbor Networks reported in a blog post.
Dealmaster: Get a 49-inch 4K Roku TV for $330
Greetings, Arsians! Courtesy of our friends at TechBargains, we have another round of deals to share. While this isn't the hottest time of year for tech deals, the Dealmaster is still digging up discounts where he can. Today we're highlighting a discount on TCL's S series Roku TVs, the 49-inch model of which is currently down to $330 on Amazon.
Yes, this TV has technically been at that price for a few weeks now, but the drop still represents a $20-30 cut for a strong budget 4K TV. In general, the tail-end of winter is a good time to buy a new set: part of that is because new models are on the horizon, but it lets those who don't need the absolute latest and greatest get a still-quality set for far less than its initial going rate. TV prices constantly cycle like that.
If you're not in the mood for a new TV, though, we've also got deals on Amazon's Fire TV boxes, lots of PCs from Dell and Alienware, Bluetooth headphones, PlayStation VR, and more. Take a look for yourself below.
Microgamer Is A Micro:Bit Handheld Console
The BBC micro:bit single board ARM computer aimed at education does not feature as often as many of its competitors in these pages. It’s not the cheapest of boards, and interfacing to it in all but the most basic of ways calls for a slightly esoteric edge connector. We’re then very pleased to see that edge connector turned from a liability into a feature by [Fabien Chouteau] with his handheld console, he uses micro:bits preprogrammed with different games in the manner of game cartridges in commercial consoles.
The micro:bit sits in its edge connector on the underside of a handheld PCB above a pair of AAA batteries, while on the other side are an OLED display and the usual set of pushbuttons. It’s a particularly simple board as the micro:bit contains all the circuitry required to support its peripherals.
He’s coded the games using the Arduino IDE with a modified version of the Arduboy2 library that allows him to easily port Arduboy games written for Arduino hardware. It’s a work in progress as there are a few more features to incorporate, but the idea of using micro:bits as cartridges is rather special. There is a video of the console in action, which we’ve placed below the break.
If the micro:bit piques your interest, you might like to take a read about its software stack, and have a look at our review.
Fail of the Week: The Little Ultrasonic Knife That Couldn’t
We all know the feeling of an idea that sounded great when it was rattling around in our head, only to disappoint when we actually build the thing. It’s a natural consequence of trying new stuff, and when it happens, we salvage what we can and move on, hopefully in wisdom.
The thing that at least semi-defeated [This Old Tony] was an attempt to build an ultrasonic cutter, and it didn’t go well. Not that any blood was shed in the video below, although there seemed like there would be the way [Old Tony] was handling those X-Acto blades. His basic approach was to harvest the transducer and driver from a cheap ultrasonic cleaner and retask the lot into a tool to vibrate a knife rapidly enough to power it through tough materials with ease.
Spoiler alert: it didn’t work very well. We think the primary issue was using a transducer that was vastly underpowered compared to commercial (and expensive) ultrasonic cutters, but we suspect the horn he machined was probably not optimized either. To be fair, modeling the acoustic performance of something like that isn’t easy, so we can’t expect much. But still, it seems like the cutter could have worked better. Share your thoughts on how to make version 2.0 better in the comments.
The video is longish, but it’s as entertaining as any of [Old Tony]’s videos, and packed full of incidental gems, like the details of cavitation. We enjoyed it, even if the results were suboptimal. If you want to see a [This Old Tony] project that really delivers, check out his beautiful boring head build.
Learn How To Read Capacitors
Engineering.com recently released a great guide for reading markings on capacitors. Check it out if you haven't seen it already!
The post Learn How To Read Capacitors appeared first on Make: DIY Projects and Ideas for Makers.
Feel Weight In Virtual Reality with this Transforming Controller
Giving players a greater sense of weight and touch is a hot topic in virtual reality right now. It only makes sense that makers would jump at the problem.
The post Feel Weight In Virtual Reality with this Transforming Controller appeared first on Make: DIY Projects and Ideas for Makers.
Galaxy S9 hands on—Samsung fixes the biggest flaw of the Galaxy S8
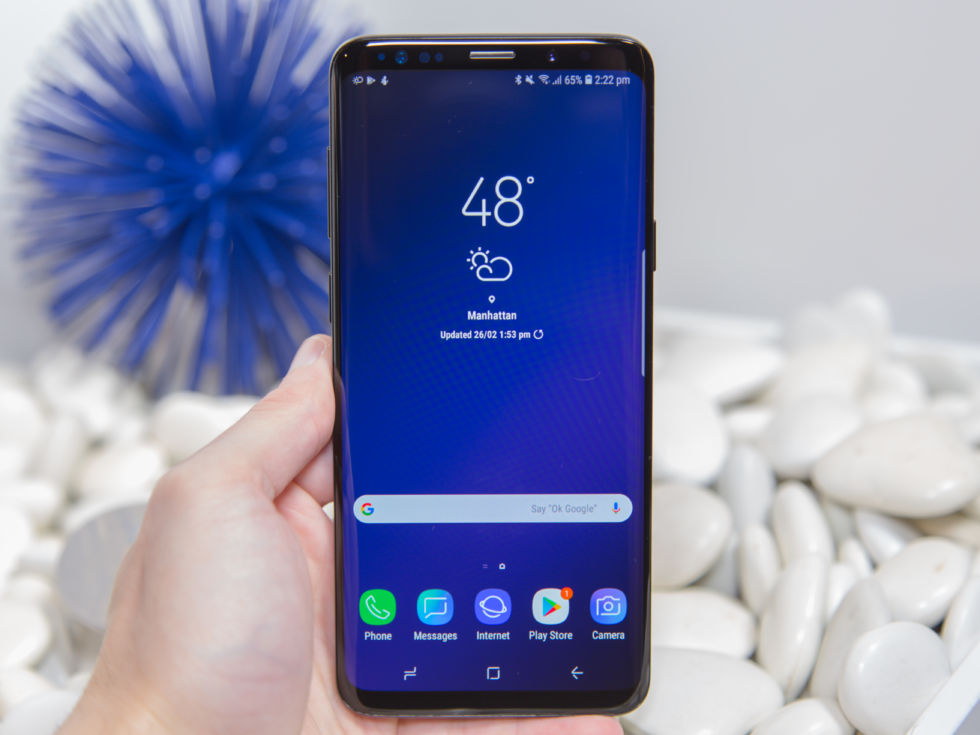
Ron Amadeo
NEW YORK—Samsung announced the Galaxy S9 to the world this week, and recently we were able to get our hot little hands on Samsung's latest. The phone is very much a Galaxy S8 with some upgrades; you can get the basic info here.
The thing I was most interested in trying out was the fingerprint reader placement, which is new this year. When Samsung switch to a slim bezel design with the Galaxy S8, the fingerprint reader needed to move to the back. Rather than place it in an easily reachable position, Samsung opted to stick it on the side of the camera module. As a result, the fingerprint reader was difficult to reach from a normal hand position, making the fingerprint reader feel like an afterthought.
Investigating the World’s Rarest Game Boy
Early last year, a very unique Game Boy Color showed up on Chinese shopping site Taobao. Rather than the rather anemic-looking display of the original GBC, this version was modified with a modern IPS LCD. Even in the pictures shown on the product page, it was clear the display on this unit was far more advanced than anything Nintendo ever packed into a Game Boy. The retro gaming community went wild, and soon the site was overwhelmed with orders. The majority of the sales were canceled by the seller, and it’s believed as few as 75 of these hacked GBCs were actually shipped out.
Thanks to one of his viewers, [Colin] was able to get his hands on one of these extremely rare customized handhelds. Clearly a man after our own heart, his first inclination was to tear the thing apart and see how they built it. While he had a fairly good idea of how they managed this hybrid of modern and classic technology, there were a couple of surprises inside.
The device has a completely stock main board, and as such works and plays like a normal GBC. But upon flipping the main board over, [Colin] found a nest of thin magnet wire connecting the new display controller to individual buttons on the front panel. As he later confirmed when he reassembled the system, this allows the user to adjust the display’s brightness by holding “Select” and using the directional pad.
As for the screen itself, the big surprise was that it’s clearly pulled out of a relatively recent smartphone. The screen is physically much larger than the opening in the GBC’s front panel, but through some software trickery the image is displayed only in the area that’s visible to the player. [Colin] managed to get a hold of a few contacts “in the know” who confirmed to him that both the hardware and software for the display controller were specifically created for this application, and are unlikely to be duplicated by anyone else.
Considering most of the Game Boy hacks we cover are about somebody jamming modern hardware into them, it’s an interesting change of pace to see a group that was so adamant about retaining as much original hardware as possible while still managing to improve the user experience.
[Thanks to Doc Oct for the tip]
Reverse Engineering Opens Up the Samsung Gear VR Controller
We love a bit of reverse engineering here at Hackaday, figuring out how a device works from the way it communicates with the world. This project from [Jim Yang] is a great example of this: he reverse-engineered the Samsung Gear VR controller that accompanies the Gear VR add-on for their phones. By digging into the APK that links the device to the phone, he was able to figure out the details of the Bluetooth connection that the app uses to connect to the device. Specifically, he was able to find the commands that were used to get the device to send data, and was able to read this data to determine the state of the device. He was then able to use this to create his own web app to use this data.
This fits in with his intention: to be able to use the Gear VR controller without the Samsung app. He did this using Web Bluetooth, which allows a web app to discover and connect to Bluetooth devices without requiring a native app. It’s a pretty new standard, so Google Chrome is the only browser that supports it at the moment. His example uses this standard to read and display the orientation of a Gear VR Controller on a web page, and he has published the code that makes this possible.
If you are looking for a cheap way to add a motion controller to a project, this would be a great place to start: you can pick up one of the Gear VR Controllers on Amazon for less than $17, and the code allows you to read button presses, touches on the touchpad and the orientation of the controller itself. That’s a lot easier than building your own controller.
Quantifying Latency in Cheap RC Transmitters
For those just starting out in the world of RC, a low cost transmitter like the Flysky FS-i6S can be very compelling. But is buying a cheap transmitter setting yourself up for failure down the line? The general feel in the RC community has been that cheaper transmitters have higher latency or “lag” on their inputs, which is precisely the kind of thing you want to avoid when flying along at 40+ MPH. As such, the general wisdom has been that your transmitter is one area where you don’t want to cheap out.
Wanting to put that theory to the test, [Marek Baczynski] set out to compare the response time between the Flysky FS-i6S and the more established Taranis X9D. In the video after the break, he uses his Saleae logic analyzer to time how long it takes movement on the transmitter sticks to get interpreted as servo commands at the receiver.
[Marek] connects the logic analyzer directly to the gimbals of both transmitters, allowing him to see user input before any processing is done by the electronics. It’s particularly interesting to see how the smooth analog curves of the gimbals are converted to a “staircase” digital output.
The final results of the latency test end up being fairly surprising. To put it simply: the cheaper Flysky radio not only more accurately interprets the user’s input, but does it considerably faster than the Taranis. [Marek] says he was so surprised by these results that he re-ran the test three times to verify.
But even taking into account the apparently higher fidelity of the cheap radio, he cautions you shouldn’t swap out your gear just yet. Higher end transmitters have a number of other features which make them worth hanging on to, even if the newer generation of radios is slightly faster. The real takeaway from this video is that if you’re just getting into the RC game, these cheaper transmitters aren’t necessarily the kiss of death the community makes them out to be.
Experiments like this and the recent detailed analysis of common hobby motors show just how seriously people take the world of RC. It’s unlikely this single experiment will quell the debate about “cheap” RC transmitters, but perhaps it’s a start.
Crankshaft: Open Source Car Computer
Modern cars and head units are pretty fancy gadget-wise. But what if your car still has an 8-track? No problem. Just pick up a Raspberry Pi 3 and a seven-inch touchscreen, and use Crankshaft to turn it into an Android Auto setup.
The open source project is based on OpenAuto which, in turn, leverages aasdk. The advantage to Crankshaft is it is a plug-and-play distribution. However, if you prefer, you can build it all yourself from GitHub.
The only limitation we can see stems from the lack of audio input on the Raspberry Pi, though we wonder if a USB sound card would take care of that problem. If you have a spare Pi and a screen hanging around, this is a handy project. A 3D-printed Pi case and some kind of mount for the LCD and you can ditch the 8-track. Not to mention with the Pi under there and all the source code, this should be highly hackable.
Perhaps you’ll do a little dashboard surgery. If you have a double DIN opening already, it might not be very difficult.
Monday, February 26
11 Chef Skills Learned While Making Fresh Lasagna
Alex makes fresh lasagna and touches on 11 essential chef skills along the way.
The post 11 Chef Skills Learned While Making Fresh Lasagna appeared first on Make: DIY Projects and Ideas for Makers.