Saturday, June 30
Sonar in Your Hand
Sonar measures distance by emitting a sound and clocking how long it takes the sound to travel. This works in any medium capable of transmitting sound such as water, air, or in the case of FingerPing, flesh and bone. FingerPing is a project at Georgia Tech headed by [Cheng Zhang] which measures hand position by sending soundwaves through the thumb and measuring the time on four different receivers. These readings tell which bones the sound travels through and allow the device to figure out where the thumb is touching. Hand positions like this include American Sign Language one through ten.
From the perspective of discreetly one through ten on a mobile device, this opens up a lot of possibilities for computer input while remaining pretty unobtrusive. We see prototypes which are more capable of reading gestures but also draw attention if you wear them on a bus. It is a classic trade-off between convenience and function but this type of reading is unique and could combine with other bio signals for finer results.
Thank you, [QES], for the tip.
Porsche shatters the Nürburgring record we thought was unbreakable
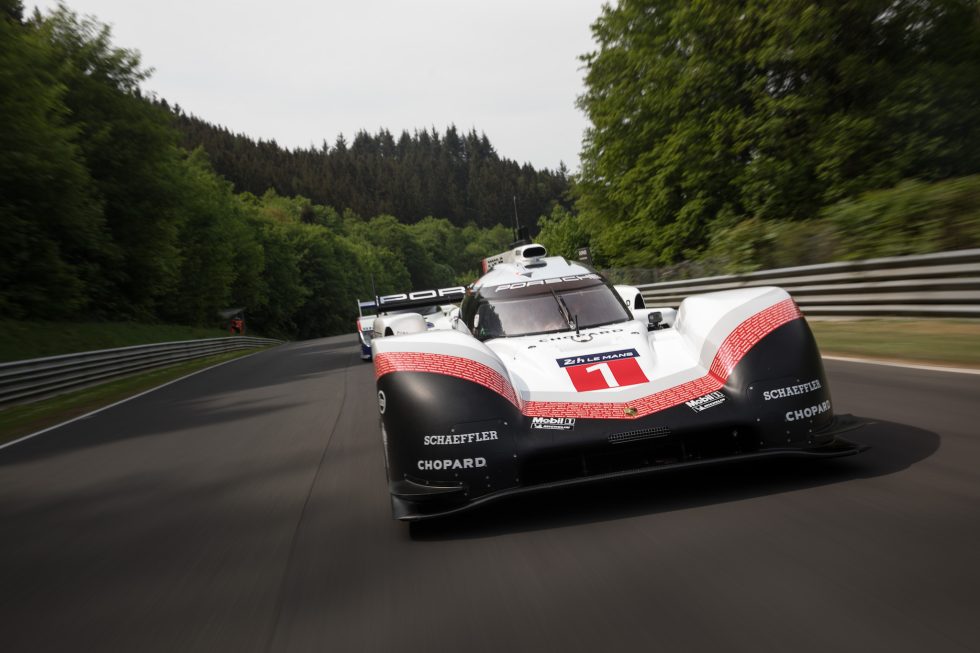
There must be something in the air. On Friday, we brought you news about Romain Dumas and Volkswagen breaking records at the Pikes Peak International Hill Climb. Just five days after Dumas' made it to the top of the mountain, his colleagues at Porsche Motorsport—the team with which he won Le Mans in 2016—have gone and shattered another record some thought would never be broken. The track is the 12.9-mile (20.8km) Nürburgring Nordschleife, and Porsche factory driver Timo Bernhard drove a Porsche 919 Evo around it in just 5:19.55.
35 years ago
Until now, the fastest man to ever lap the Nordschleife was the late Stefan Bellof. By the time of his run in 1983, the track was considered too dangerous for Formula 1, but little else had changed since the 1920s. Nordschleife was still workable for Group C though, which held its 1983 1000kms of Nürburgring there. During qualifying for the race, Bellof—driving a works Porsche 956—lapped the place in 6:11.13. (There's no in-car footage of his run, but teammate Derek Bell did carry a camera for a practice lap that isn't that much slower.)
Gyrotourbillion Blesses The Eyes, Hard to Say
Clock movements are beautifully complex things. Made up of gears and springs, they’re designed to tick away and keep accurate time. Unfortunately, due to the vagaries of the universe, various sources of error tend to creep in – things like temperature changes, mechanical shocks, and so on. In the quest for ever better timekeeping, watchmakers decided to try and rotate the entire escapement and balance wheel to counteract the changing effect of gravity as the watch changed position in regular use.
They’re mechanical works of art, to be sure, and until recently, reserved for only the finest and most luxurious timepieces. As always, times change, and tourbillions are coming down in price thanks to efforts by Chinese manufacturers entering the market with lower-cost devices. But hey – you can always just make one at home.
That’s right – it’s a 3D printed gyrotourbillion! Complete with a 3D printed watch spring, it’s an amazing piece of engineering that would look truly impressive astride any desk. All that’s required to produce it is a capable 3D printer and some off-the-shelf bearings and you’ve got a horological work of art.
It’s not the first 3D-printed tourbillion we’ve seen, but we always find such intricate builds to be highly impressive. We can’t wait to see what comes next – if you’re building one on Stone Henge scale for Burning Man, be sure to let us know. Video after the break.
[Thanks to Keith for the tip!]
One-upping the NES Classic Edition with the Raspberry Pi 3 and RetroPie
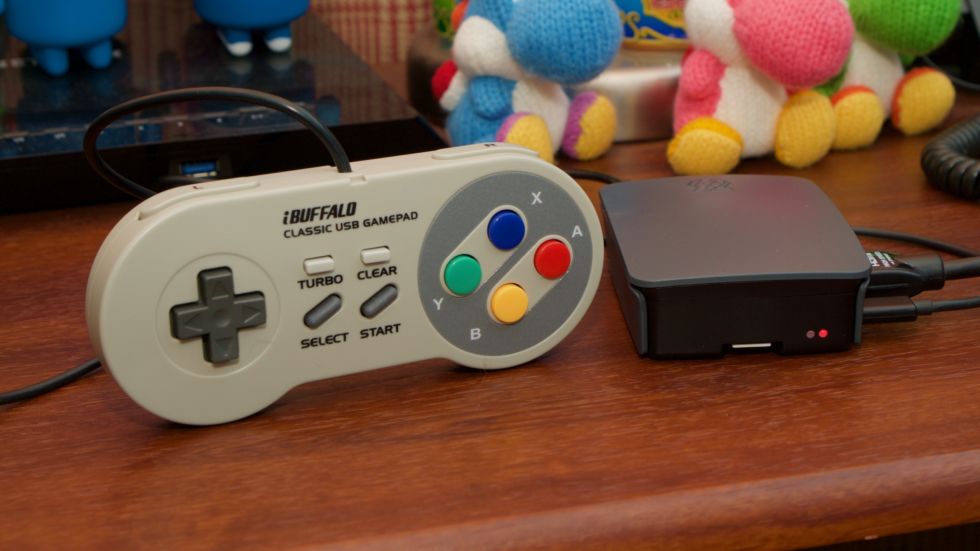
Andrew Cunningham
In November 2016, Nintendo surprised everyone by going back to its roots and releasing the NES Classic. The delightful emulator/nostalgia-fest sparked unanticipated demand, including near-instant supply issues and 200-percent-plus markups in secondary markets. So in December of 2016, we decided to build our own version instead.
Last April, Nintendo bizarrely halted sales of the hot-selling retro console, sparking us to resurface this guide. And with the news that Nintendo relaunched the console this week—but yet again supply is an early hurdle for interested gamers—we're re-running this piece to help those of you with a DIY streak once build your own, more flexible alternative. Hardware recommendations have been updated and lightly edited to reflect current availability and pricing for June 2018.
Against my better judgment, I’ve tried a couple of times to snag one of those adorable little $60 mini NES Classic Editions—once when Amazon put some of its limited stock online and crashed its own site, and once when Walmart was shipping out small quantities every day a couple of weeks ago. In both cases, I failed.
But the dumb itch of nostalgia can’t always be scratched by logical thoughts like “do you really need to pay money for Super Mario Bros. 3 again,” and “Castlevania II: Simon’s Quest is probably the weakest of the three NES Castlevania games.” Since it’s not entirely clear if or when those little mini NESes will become readily available, I decided to funnel that small wad of expendable cash and the desire for some nostalgia-fueled gaming into a DIY project.
The BBC Computer Literacy Project From The 1980s Is Yours To Browse
In the early 1980s there was growing public awareness that the microcomputer revolution would have a significant effect on everybody’s lives, and there was a brief period in which anything remotely connected with a computer attracted an air of glamour and sophistication. Broadcasters wanted to get in on the act, and produced glowing documentaries on the new technology, enthusiastically crystal-ball-gazing as they did so.
In the UK, the public service BBC broadcaster produced a brace of series’ over the decade probing all corners of the subject as part of the same Computer Literacy Project that gave us Acorn’s BBC Micro, and we are lucky enough that they’ve put them all online so that we can watch them (again, in some cases, if a Hackaday scribe can get away with revealing her age).
You can see famous shows such as the moment when the presenters experienced a live on-air hack while demonstrating an early online service, but most of it is a fascinating contemporary look at the computers we now enthuse over as retro devices. Will the MSX sweep all before it, for example? (It didn’t).
They seem very dated now with their 8-bit micros (if not just for the word “micro”), synth music, and cheesy graphics. But what does come across is the air of optimism, this was the future, and it was packaged not as a threat, but as a good place to be. Take a look, but make sure you have plenty of time. You may spend a while in front of the screen.
We’ve mentioned int he past another spin-off from the Computer Literacy Project, the Domesday Project.
Thanks [Darren Grant] for the tip.
Exostiv FPGA Debugging Might be a Bargain
Got $4,000 to spend? Even if you don’t, keep reading — especially if you develop with FPGAs. Exostiv’s FPGA debugging setup costs around $4K although if you are in need of debugging a complex FPGA design and your time has any value, that might not be very expensive. Then again, most of us have a lot of trouble justifying a $4,000 piece of test gear. But we wanted to think about what Exostiv is doing and why we don’t see more of it. Traditionally, debugging FPGAs meant using JTAG and possibly some custom blocks that act like a logic analyzer and chew up real estate on your device. Exostiv also uses some of your device, but instead of building a JTAG-communicating logic analyzer it… well, here’s what their website says:
EXOSTIV IP uses the MGTs (Multi-Gigabit Transceivers) to flow captured data out of the FPGA to an external memory. EXOSTIV IP supports repeating captures of up to 32,768 internal nodes simultaneously at the FPGA’s speed of operation (16 data sets x 2,048 bits).
EXOSTIV IP provides dynamic multiplexer controls to capture even more data sets without the need to recompile. Dynamic ON/OFF controls of data sets let you select the data set and preserve the MGT’s bandwidth for when deeper captures of a reduced set of data is required.
In a nutshell, this means they use high-speed communications to send raw data to a box that has memory and connects back to a PC. That means they can store more data, have more data come out of the chip over a certain time frame, and do sophisticated processing. You can see a video about the device below, and there are more detailed videos on their channel, as well.
There are two things you might be wondering. First, why not just send the data to the PC instead of an intermediate box. Notice the box has a USB 3 connection back to the PC. That’s fast, but it isn’t fast enough.
The other thing you might be wondering is why you’ve read this far since your boards don’t have MGTs and you don’t have $4,000 sitting around to buy a debugging tool. But it occurs to us, that while the implementation of this idea is very robust-seeming, there’s no reason we couldn’t adapt it to our FPGA designs. Why haven’t we seen a hacker design that uses a reasonably cheap and fast I/O (maybe LVDS) to pipe data to an Arm board with some memory. In fact, you would think you could separate the modules for the FPGA so you’d have a core and a communication channel that would allow different features.
Of course, open source debug cores are not unheard of, but they tend to work like traditional JTAG debuggers where you essentially build a logic analyzer on the spare parts of your FPGA. We haven’t seen anything like the Exostiv solution. Probably the closest we’ve seen is this device from Cornell, but it displays on a VGA monitor. There’s also no shortage of standalone logic analyzers that use FPGAs.
Charging An Electric Supercar With Lemons, Kids, And The Sun
First things first: the tease on this video, that an electric supercar can be charged from a massive lemon battery array, is exactly that – a tease. Despite that, it makes for an interesting story and a great attempt to get kids exposed to science and engineering.
The story goes that [Mark] was approached by Volkswagen to help charge the batteries on their entry for the upcoming Pikes Peak International Hill Climb, the annual “Race to the Clouds” in Colorado. Racers are tortured by a 4,700′ (1,440 m) vertical climb over a 12.42 mile (20 km) course that features 156 switchback turns. Volkswagen’s entry is an electric supercar, and they sent [Mark] a portable battery cart to charge up the best way he saw fit.
Teaming up with [William Osman], the first attempt was a massive array of lemon cells, made with waterjet-cut strips of zinc and copper held in a plywood frame. Studded with 1,232 lemons, the battery performed just about as well as you’d expect it would. Plan B was cute, and another of [Mark]’s attempts to pad his “Funnest Uncle Ever” score a bit. He devised a zip line with regenerative braking to charge a cordless drill battery, and then indirectly harvested the energy in the battery by turning it into lemonade for a bunch of kids. The sugared-up kids rode the zip line till the battery was charged.
That was still a drop in the bucket, though, so Plan C saw [Mark] install a large solar array on his roof; the tie-in here was that the lemon-powered kids got to design a cleaning system for the solar array. A weak link, to be sure, but the kids had fun, and we can’t deny that the car will at least be partially lemon-powered when it heads up the hill.
Free E-Book: Software Defined Radio for Engineers
We really like when a vendor finds a great book on a topic — probably one they care about — and makes it available for free. Analog Devices does this regularly and one you should probably have a look at is Software Defined Radio for Engineers. The book goes for $100 or so on Amazon, and while a digital copy has pluses and minuses, it is hard to beat the $0 price.
The book by [Travis F. Collins], [Robin Getz], [Di Pu], and [Alexander M. Wyglinski] covers a range of topics in 11 chapters. There’s also a website with more information including video lectures and projects forthcoming that appear to use the Pluto SDR. We have a Pluto and have been meaning to write more about it including the hack to make it think it has a better RF chip inside. The hack may not result in meeting all the device specs, but it does work to increase the frequency range and bandwidth. However, the book isn’t tied to a specific piece of hardware.
Make no mistake, the book is a college-level textbook for engineers, so it isn’t going to go easy on the math. So if the equation below bugs you, this might not be the book you start with:
[Di Pu] and [Alexander Wyglinksi] have an older similar book, and it looks like the lecture videos are based on that book (see video below). The projects section on the website doesn’t appear to have any actual projects in it yet, although there are a couple of placeholders.
We have enjoyed Analog’s book selections in the past including The Scientist and Engineer’s Guide to Digital Signal Processing which is a classic. If you visit their library you’ll find lots of books along with classes and videos, too.
If you want something a bit less academic, there’s always [Ossmann’s] videos. Or if you’d rather just use an SDR, there are plenty of inexpensive options to choose from.
Handmade Robot Brings Stop Motion to Life
Stop motion animation is often called a lost art, as doing it (or at least, doing it well) is incredibly difficult and time consuming. Every detail on the screen, no matter how minute, has to be placed by human hands hundreds of times so that it looks smooth when played back at normal speed. The unique look of stop motion is desirable enough that it still does get produced, but it’s far less common than hand drawn or even computer animation.
If you ever wanted to know just how much work goes into producing even a few minutes of stop motion animation, look no farther than the fascinating work of [Special Krio]. He not only documented the incredible attention to detail required to produce high quality animation with this method, but also the creation of his custom robotic character.
Characters in stop motion animation often have multiple interchangeable heads to enable switching between different expressions. But with his robotic character, [Special Krio] only has to worry about the environments, and allow his mechanized star do the “acting”. This saves time, which can be used for things such as making 45 individual resin “drops” to animate pouring a cup of tea (seriously, go look).
To build his character, [Special Krio] first modeled her out of terracotta to get the exact look he wanted. He then used a DIY 3D laser scanner to create a digital model, which in turn he used to help design internal structures and components which he 3D printed on an Ultimaker. The terracotta original was used once again when it was time to make molds for the character’s skin, which was done with RTV rubber. Then it was just the small matter of painting all the details and making her clothes. All told, the few minutes of video after the break took years to produce.
This isn’t the first time we’ve seen 3D printing used to create stop motion animation, but the final product here is really in a league of its own. It reminds us of that 3D printed stop motion film [Bre Pettis] was working on, but you know, a real thing and not just a publicity stunt.
[Thanks to Antonio for the tip.]
Friday, June 29
R/C Rocket-Beest Burns Up Fuses Out There Alone
We’re beginning to think the “S” in [Jeremy S Cook] stands for strandbeest. He’ll be the talk of the 4th of July picnic once he brings out his latest build—a weaponized, remote-controlled strandbeest that shoots bottle rockets. There are a bank of money shots up on Imgur.
This ‘beest is the natural next step after his remote-controlled walker, which we featured a month or so ago. Like that one, the locomotion comes from a pair of micro gear motors that are controlled by an Arduino Nano over Bluetooth. The pyrotechnics begin when nitinol wire cleverly strung across two lever nuts is triggered. All the electronics are housed inside a 3D-printed box that [Jeremy] designed to sit in the middle of the legs. We love the face plate he added later in the build, because those gumdrop LED eyes are sweet.
Can you believe that this vehicle of destruction began as a pile of innocent, pasta-colored pieces of kit? We dig the camouflaged battleship paint job, ’cause it really toughens up the whole aesthetic. And really, that’s probably what you want if you’re driving around a spindly beast that can just shoot rockets whenever. Let’s light this candle after the break, shall we?
Tips of the Week: Popsicle Sanding Sticks, Swapable Work Surfaces, Wall Framing Trick, Wire Splicing to NASA Standards
Another week of seriously useful and thought-provoking tips from the maker community.
The post Tips of the Week: Popsicle Sanding Sticks, Swapable Work Surfaces, Wall Framing Trick, Wire Splicing to NASA Standards appeared first on Make: DIY Projects and Ideas for Makers.
Maker Faire Prague Highlights Czech Makers
Last weekend, June 23-24 Prague hosted its very first Maker Faire and the first ever in the Czech Republic.
The post Maker Faire Prague Highlights Czech Makers appeared first on Make: DIY Projects and Ideas for Makers.
When The Going Gets Tough, These Wheels Transform To Tracks
When we want to build something to go where wheels could not, the typical solution is to use tracks. But the greater mobility comes with trade-offs: one example being tracked vehicles can’t go as fast as a wheeled counterpart. Information released by DARPA’s ground experimental vehicle technology (GXV-T) program showed what might come out of asking “why can’t we switch to tracks just when we need them?”
This ambitious goal to literally reinvent the wheel was tackled by Carnegie Mellon’s National Robotics Engineering Center. They delivered the “Reconfigurable Wheel-Track” (RWT) that can either roll like a wheel or travel on its tracks. A HMMWV serves as an appropriate demonstration chassis, where two or all four of its wheels were replaced by RWTs. In the video (embedded below) it is seen quickly transforming from one mode to another while moving. An obviously desirable feature that looks challenging to implement. This might not be as dramatic of a transformation as a walking robot that can roll up into a wheel but it has the advantage of being more immediately feasible for human-scale vehicles.
The RWT is not the only terrain mobility project in this DARPA announcement but this specific idea is one we would love to see scaled downed to become a 3D-printable robot module. And though our Hackaday Prize Robotics Module Challenge has already concluded, there are more challenges still to come. The other umbrella of GXV-T is “crew augmentation” giving operators better idea of what’s going around them. The projects there might inspire something you can submit to our upcoming Human-Computer Interface Challenge, check them out!
[via The Drive]
Linux Fu: Scripting for Binary Files
If you ever need to write a binary file from a traditional language like C, it isn’t all that hard to do. About the worst thing you might have to deal with is attempts to fake line endings across Windows and Linux, but there’s usually a way to turn that off if it is on by default. However, if you are using some type of scripting language, binary file support might be a bit more difficult. One answer is to use a tool like xxd or t2b (text-to-binary) to handle the details. You can find the code for t2b on GitHub including prebuilt binaries for many platforms. You should be able to install xxd from your system repository.
These tools take very different approaches. You might be familiar with tools like od or hexdump for producing readable representations of binary files. The xxd tool can actually do the same thing — although it is not as flexible. What xxd can even reverse itself so that it can rebuild a binary file from a hex dump it creates (something other tools can’t do). The t2b tool takes a much different approach. You issue commands to it that causes it to write an original hex file.
Both of these approaches have some merit. If you are editing a binary file in a scripting language, xxd makes perfect sense. You can convert the file to text, process it, and then roll it back to binary using one program. On the other hand, if you are creating a binary file from scratch, the t2b program has some advantages, too.
I decided to write a few test scripts using bash to show how it all works. These aren’t production scripts so they won’t be as hardened as they could be, but there is no reason they couldn’t be made as robust as you were willing to make them.
Cheating a Little
I decided to write two shell scripts. One will generate an image file. I cheated in two ways there. First, I picked the PPM (Portable Pix Map) format which is very simple to create. And second I ignored the format that uses ASCII instead of binary. That’s not strictly cheating because it does make a larger file, as you’d expect. So there is a benefit to using the binary format.
The other script takes a file in the same format and cuts the color values within it by half. This shows off both tools since the first job is generating an image file from data and the second one is processing an image file and writing out a new one. I’ll use t2b for the first job and xxd for the second.
PPM File Format
The PPM format is part of a family of graphics formats from the 1980s. They are very simple to construct and deconstruct, although they aren’t known for being small. However, if you needed to create a graphic from a Raspberry Pi program, it is sometimes handy to create them using this simple file format and then use ImageMagick or some other tool to convert to a nicer format like PNG.
There are actually three variants of the format. One for black and white, one for grayscale, and another for color. In addition, each of them can contain ASCII data or binary data. There is a very simple header which is always in ASCII.
We’ll only worry about the color format. The header will start with the string “P6.” That usually ends with a newline, although defensively, you ought to allow for any whitespace character to end the header fields. Then the X and Y limits — in decimal and still in ASCII — appear separated by whitespace. This is usually really a space and a newline at the end. The next part of the header is another ASCII decimal value indicating the maximum value for the color components in the image. After that, the data is binary RGB (red/green/blue) triplets. By the way, if the P6 had been a P3, everything would remain the same, but the RGB triplets would be in ASCII, not binary. This could be handy in some cases but — as I mentioned — will result in a larger file.
Here’s a sample header with a little bit of binary data following it:
The green text represents hex numbers and the other boxes contain ASCII characters. You can see the first 15 bytes are header and after that, it is all image data.
T2B
The t2b program takes a variety of commands to generate output. You can write a string or various sizes of integers. You can also do things like repeat output a given number of times and even choose what to output based on conditions. There’s a way to handle variables and even macros.
As an example, my script will write out an image with three color bars in it. The background will be black with a white border. The color bars will automatically space to fit the box. I won’t use too many of the t2b features, but I did like using the macros to make the resulting output easier to read. Here’s the code for creating the header (with comments added):
strl P6 # Write P6 followed by a newline (no quotes needed because no whitespace in the string) str $X # Write the X coordinate (no newline) u8 32 # a space strl $Y # The Y coordinate (with newline) strl 255 # Maximum subpixel value (ASCII)
That’s all there is to it. The RGB triples use the u8 command, although if you could probably use a 24-bit command, too. I also set up some macros for the colors I used:
macro RED begin u8 255 times 2 u8 0 endtimes endmacro
Once you have the t2b language down, the rest is just math. You can find the complete code on GitHub, but you’ll see it just computes 7 equal-sized regions and draws different colors as it runs through each pixel in a nested set of for loops. There’s also a one-pixel white border around the edges for no good reason.
When you want to run the code you can either specify the X and Y coordinates or take the 800×600 default:
./colorbar.sh 700 700 | t2b >outputfile.ppm
If you intercept the output before the t2b program, you’ll see the commands rolling out of the script. Here’s the default output to the ppm file:
Shades of Gray
The other script is a little different. The goal is to divide all the color values in a PPM file in half. If it were just binary data, that would be easy enough, but you need to skip the header so as not to corrupt it. That takes a little extra work. I used gawk (GNU awk) to make the work a little simpler.
The code expects output from xxd, which looks like this:
00000000: 5036 0a38 3030 2036 3030 0a32 3535 0aff P6.800 600.255.. 00000010: ffff ffff ffff ffff ffff ffff ffff ffff ................ 00000020: ffff ffff ffff ffff ffff ffff ffff ffff ................ 00000030: ffff ffff ffff ffff ffff ffff ffff ffff ................ 00000040: ffff ffff ffff ffff ffff ffff ffff ffff ................
The address isn’t important to us. You can ask xxd to suppress it, but it is also easy to just skip it. The character representations to the right aren’t important either. The xxd program will ignore that when it rebuilds the binary. Here’s the code in awk (which is embedded in the shell script):
# need to find 4 white space fields BEGIN { noheader=4 } { lp=1 } { split($0, chars, "") # skip initial address while (chars[lp++]!=":"); n=0; # # of bytes read # get two characters while (n<16 && lp<length(chars)) { # heuristically two space characters out of xxd ends the hex dump line (ascii follows) if (chars[lp] ~ /[ \t\n\r]/) { if (chars[++lp] ~ /[ \t\n\r]/) { break; # no need to look at rest of line } } b=chars[lp++] chars[lp++]; n++; # if header then skip white space if (noheader>0) { if (b=="20" || b=="0a" || b=="0d" || b=="09") noheader--; } else { # if not header than /2 bn=strtonum("0x" b)/2; bs=sprintf("%02x",bn); chars[lp-2]=substr(bs,1,1); chars[lp-1]=substr(bs,2,1); } } # recombine array and print p="" for (i=1;i<=length(chars);i++) p=p chars[i]; print p }
The awk code simply skips the address and then pulls up to 16 items from a line of data. The first task is to count whitespace characters to skip over the header. I made the assumption that there would not be runs of whitespace, although a more robust program would probably consume multiple spaces (easy to fix). After that, each byte gets divided and reassembled. This task is more character oriented and awk doesn’t handle characters well without a trick.
In particular, I used the split command to convert the current line into an array with each element containing a character. This includes any whitespace characters because I used an empty string as the split delimiter:
split($0, chars, "")
After processing the array — which isn’t hard to do — you can build a new string back like this:
p="" for (i=1;i<=length(chars);i++) p=p chars[i];
The output file will feed back to xxd with the -r option and you are done:
xxd infile.ppm | ./half.sh | xxd -r >outfile.ppm
Two is the Loneliest
This is a great example of how the Unix philosophy makes it possible to build tools that are greater than the sum of their parts. A simple program changes a text-processing language like awk into a binary file manipulation language. Great. By the way, if your idea of manipulating binary is Intel hex or Motorola S records, be sure to check out the srec_cat and related software which can manipulate those, too.
Once you have a bunch of binary files, you might appreciate an online hex editor. By the way, a couple of years ago, I mentioned using od to process binary files in awk. That’s still legitimate, of course, but xxd allows you to go both ways, which is a lot more useful.
Trash Panda Brings A Robotic Twist To Games
A great example of fun and simple robotics made with CRICKIT from Adafruit.
The post Trash Panda Brings A Robotic Twist To Games appeared first on Make: DIY Projects and Ideas for Makers.
How to Detect Hidden Cameras
Be aware of what might be peeping on you
The post How to Detect Hidden Cameras appeared first on Make: DIY Projects and Ideas for Makers.
A LIDAR Scanner Build in Glorious Detail
LIDAR is a very exciting technology that is only just now starting to become accessible to the DIY market. Think radar, but with lasers. There’s a few different modules starting to pop up for just a few hundred dollars. But what is one to do with a LIDAR module? Well, [David] decided to build a room scanner with his Garmin LIDAR Lite, and it’s a wonderful sight to behold.
The scanner consists of a rotating platform, which is driven by a stepper motor. The platform then contains a second motor which runs a tilt axis, upon which the LIDAR is mounted. By aiming the LIDAR in various directions, and recording the detected range, it’s possible to build a point cloud representation of the surrounding area.
The build uses a couple of STM32 chips to do motor control and interface with the LIDAR, but where this build really shines is the mechanical side of things. [David] goes into serious detail about the machining of the parts that make up the rotating system, and there’s plenty of cool bits and pieces like slip rings to make it all work. There’s even some home casting going on here! Be warned, though: there’s some rather juicy close-ups of lathes in action, so put the kids to bed before watching this one all the way through.
We love to see a well-executed build, and even more so when we get to watch the intricate details of how it came together. If you’re still looking for some more inspiration, we’ve seen other LIDAR room scanners before, too.
Box Joint Jig Does Barcodes
Woodworking is the fine art of turning dead tree carcasses into precision instruments. That means breaking out the saws and chisels and making many, many precise cuts over and over. If you have a table saw, every problem becomes a piece of wood, or something like that, and we’ve seen some fantastic jigs that make these precision cuts even easier. We’ve never seen something like this, though. It’s a box joint jig for a table saw, it’s automated, and it puts barcodes on boxes.
[Ben] built this box joint jig a few years ago as a computer-controlled device that slowly advances a piece of wood on a sled, allowing him to create precise, programmable box joints. The design is heavily influenced from [Matthias Wandel]’s screw advance box joint jig, but instead of wood gears (heh), [Ben] is using the Internet of Things. Or a Raspberry Pi, stepper motor, and a few LEDs. Same difference.
Although [Ben]’s previous box joints were all the same size, a programmable box joint jig can do some weird-looking joints. That’s where [Ben] got the idea to encode a barcode in walnut. After using a web app to create a barcode that encodes the number 255 — this is important for later — [Ben] programmed his jig to cut a few slots.
The box was finished as you would expect, but there’s a neat addition to the top. It’s a combination lock that opens when the combination is set to 255. It’s brilliant, and something that could be done with some handsaws and chisels, but this jig makes it so easy it’s hard to think the jig wasn’t explicitly designed for this project.
Carousel of Cereals Mixes and Matches Custom Breakfast Blends
There are those who reckon the humble bowl of breakfast cereal to be the height of culinary achievement. Look askance if you must, but cereal junkies are a thing, and they have a point. The magic comes not from just filling a bowl and adding a splash of milk, but by knowing which cereals to mix together.
Who needs all that fussy mixing, though, when you can automate and customize your cereal dispensing chores? That’s the approach [Kevin Obermann] and [Adrian Bernhart] took with their Cereal Dispensing Machine, even if they went a little further than necessary. Laser-cut plywood forms a four-station carousel for off-the-shelf dry-good dispensers, each of which got a stepper motor to replace the wrist-twisting. The original motors were a bit too wimpy to handle the more rugged morning selections and were eventually upgraded to gear motors. The platform that supports the dispensers also holds all the electronics, including an ESP32 to run everything and host the web app needed to choose your poison. Plus RGB LEDs, because breakfast should look like a rave. Sadly, the team ran out of GPIO pins and were unable to run the peristaltic pump needed to add the milk. There will always be version 2.0, though.
If cereal isn’t your automated breakfast of choice, we understand. Perhaps a more [Wallace] and [Gromit] style breakfast machine would do, or a robotic peanut butter sandwich any time of day is a treat.
Thursday, June 28
Samsung’s Note 9 announcement is August 9
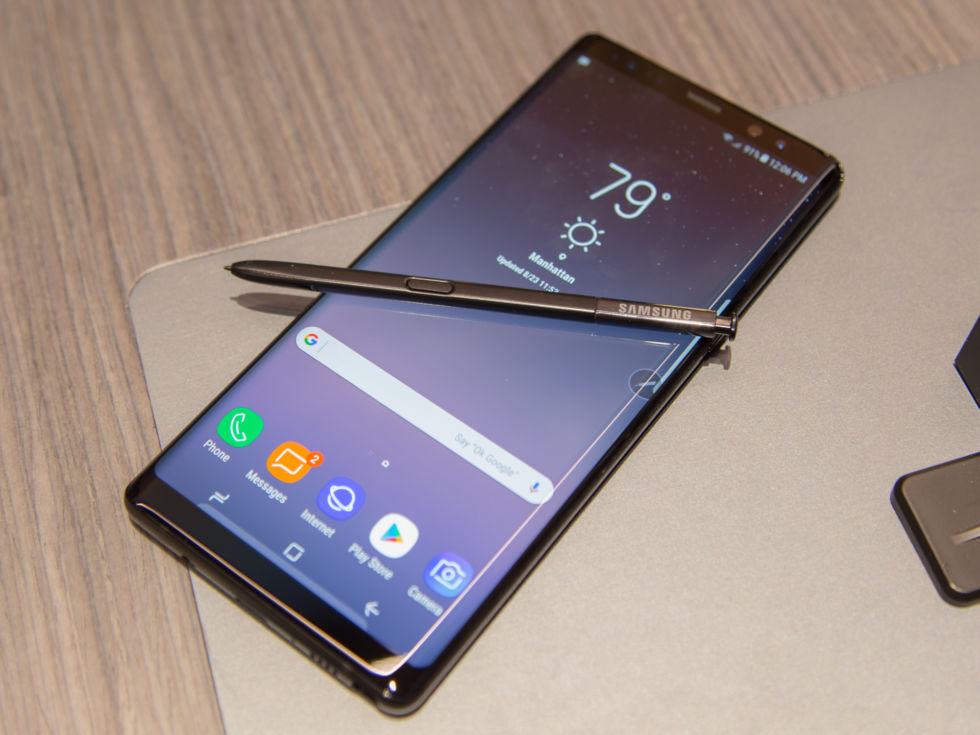
Ron Amadeo
We now know the date of the Galaxy Note 9 announcement. Samsung sent out invites to "Samsung Galaxy UNPACKED 2018" on August 9 and a teaser image showing the Note line's trademark S-Pen. This year, the show will be at the Barclays Center in New York City, the home of the NBA's Brooklyn Nets and the NHL's New York Islanders.
There isn't a huge amount of rumors out there about the Galaxy Note 9. If past Note devices any indication, the Note 9 will be very close to the latest Galaxy S9+, just with a slightly larger screen and battery, a squared-off design, an S-Pen, and some new camera tech. Sure enough, a report from Bloomberg earlier this month said the Note 9 "will look similar to last year’s model" and have "an upgraded camera." Samsung just announced a new "Isocell Plus" camera sensor, which it says can "capture more light, significantly increasing light sensitivity and color fidelity." There's a good chance it will end up in the Note 9.
3D Printed Tourniquets are Not a Cinch
Saying that something is a cinch is a way of saying that it is easy. Modeling a thin handle with a hole through the middle seems like it would be a simple task accomplishable in a single afternoon and that includes the time to print a copy or two. We are here to tell you that is only the first task when making tourniquets for gunshot victims. Content warning: there are real pictures of severe trauma. Below, is a video of a training session with the tourniquets in Hayat Center in Gaza and has a simulated wound on a mannequin.
On the first pass, many things are done correctly: the handle is the correct length and diameter, the strap hole fit the strap, and the part is well oriented on the platen. As with many first iterations, it looks good on a screen, but in the real world, we all live under Murphy’s law. In practice, some of the strap holes had sharp edges that cut into the strap, and one of the printed buckles broke unexpectedly.
On the whole, the low cost and availability of the open-source tourniquets outweigh the danger of operating without them. Open-source medical devices are not just for use in the field, they can help with training too. This tourniquet is saving people and proving that modeling skills can be a big help in the real world.
Amazon is turning its Fire tablets into portable Echo Shows
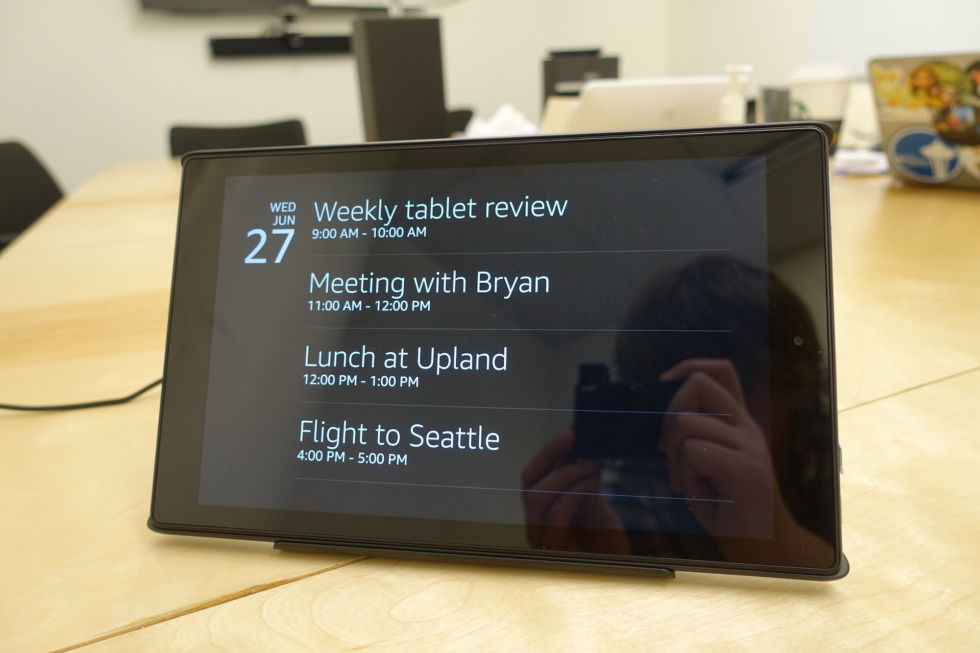
Jeff Dunn
Amazon on Thursday announced a software update for its Fire HD 8 and Fire HD 10 tablets that introduces “Show Mode,” a new setting that makes the two slates function similarly to the company’s Echo Show smart speaker.
Amazon says the update will start rolling out to the current-generation Fire HD 8 and Fire HD 10 tablets on July 2. The mode won’t be available on older Fire tablets or the less expensive Fire 7 tablet.
These Three Kits Can Help Connect Your Project to Powerful AI
now you can choose the best one for your needs
The post These Three Kits Can Help Connect Your Project to Powerful AI appeared first on Make: DIY Projects and Ideas for Makers.
DIY Braille Embosser
Build a braille embosser for a fraction of the cost of commercial machines
The post DIY Braille Embosser appeared first on Make: DIY Projects and Ideas for Makers.
Tiny Printers Get Color Mixing
Last weekend was the inaugural East Coast RepRap Festival in beautiful Bel Air, Maryland. Like it’s related con, the Midwest RepRap Festival, ERRF is held in the middle of nowhere, surrounded by farms, and is filled with only people who want to be there. It is the anti-Maker Faire; only the people who have cool stuff to show off, awesome prints, and the latest technology come to these RepRap Fests. This was the first ERRF, and we’re looking forward to next year, where it will surely be bigger and better.
One of the stand-out presenters at ERRF didn’t have a big printer. It didn’t have normal stepper motors. There weren’t Benchies or Marvins or whatever the standard test print is these days. [James] is showing off tiny printers. Half-scale printers. What’s half the size of a NEMA 17 stepper motor? A NEMA 8, apparently, something that isn’t actually a NEMA spec, and the two companies that make NEMA 8s have different bolt hole patterns. This is fun.






If these printers look familiar, you’re right. A few years ago at the New York Maker Faire, we checked out these tiny little printers, and they do, surprisingly, print. There are a lot of tricks to make a half-size printer, but the most impressive by far is the tiny control board. This tiny little board is just 2.5 by 1.5 inches — much smaller than the standard RAMPS or RAMBO you’d expect on a DIY printer. On the board are five stepper drivers, support for two heaters, headers for OLEDs and Graphic LCDs, and a switching regulator. It’s a feat of microelectronics that’s impressive and necessary for a half-size printer.
Since we last saw these tiny printers, [James] has been hard at work expanding what is possible with tiny printers. The most impressive feat from this year’s ERRF was a color-mixing printer built around the same electronics as the tiny printers. The setup uses normal-size stepper motors (can’t blame him) and a diamond-style hotend to theoretically print in three colors. If you’ve ever wanted a tiny printer, this is how you do it, and I assure you, they’re very, very cute.
How to extrapolate our tech legal future from our past and present
In recent months, not one but two Ars writers have released books, so we decided that for this month’s edition of Ars Technica Live, that we (Cyrus Farivar and Annalee Newitz) would interview each other about our respective tomes.
My book, Habeas Data, covers 50 years of surveillance law in America and chronicles the surprising effects of 10 monumental legal case that have impacted our world.
Sunny Custom Keyboard Illuminates the Past
Ever wonder why keyboard number pads and telephone dials have reversed layouts? Theories abound, but the most plausible one is that, shrug, it just happened that way. And now we’re stuck with it.
Well, that answer’s not good enough for [Jesse], so he punched up his own keyboard design that combines the golden years of function-rich Sun and IBM keyboards with Ma Bell’s DTMF number arrangement. That’s right, Sundial has 24 function keys total, and the number pad matches Ma Bell’s all the way down to the asterisk/zero/octothorpe pattern on the bottom row. How do we know what the unlabeled ones are, you ask? It’s all mapped out in this layout editor. We love that it has all the key lock indicator lights, because that practice should’ve never faded out in the first place.
Though inspired by this beautiful unicorn of an Arduino keyboard we covered a few months ago, the Sundial uses a Teensy 2.0 to translate [Jesse]’s Cherry MX clone-driven wishes into software commands. It’s also painstakingly hand-wired, so here’s the build log for you to drool over. Just cover up your keyboard first.
Wednesday, June 27
After The Sun Set On San Mateo, LED Takes Over Hackaday’s BAMF Meetup
After this Spring’s Bay Area Maker Faire closed down for Saturday night and kicked everybody out, the fun moved on to O’Neill’s Irish Pub where Hackaday and Tindie held our fifth annual meetup for fellow Maker Faire attendees. How do we find like-minded hackers in a crowded bar? It’s easy: look for tables lit by LEDs and say hello. It was impossible to see everything people had brought, but here are a few interesting samples.
The team from Misty Robotics brought their namesake product to the meetup and carried Misty when there wasn’t enough room to let the robot run. Here [Ben Edwards] is answering questions about Misty’s capabilities. The team wants their product to appeal to a wide spectrum of budding roboticists: from beginners who need a gentle on-ramp to seasoned veterans interested in modifying Misty for their own needs.
Since those who would attend a Hackaday + Tindie meetup trend towards the latter, Misty arrived with a demonstration of hackability: a 3D-printed beer glass holder has replaced the standard left arm, fitting in with the meetup’s location. It was fun to see the robot’s personality as Misty looked around and occasionally reacted to being patted on top of the touch-sensitive head.
Longtime Hackaday.io participant Joshua Snyder brought his projects RGB LED matrix and Neopixel pocket watch, giving people who have only read about his projects an opportunity to play with them in person. The Neopixel pocket watch seen below is quite the stealthy transformer — when closed and inactive, it blends in with wardrobe of another era. But when active, it is very definitely a 21st century timepiece.The RGB LED matrix also shown was pressed into service as an impromptu bar arcade.


Some of the attendees had problem finding enough table space in a crowded bar to set up, but the crew of TinyCircuits had no such worry. They were able to put their entire product line on a little round bar table and still leave plenty of room for everyone’s beer. If you’ve only seen these creations in pictures, it’s hard to appreciate how tiny they actually are. It takes some hands-on time for the size to really sink in, and this table is always crowded with people clicking tiny buttons with their fingernails.
Hackaday’s own Kerry Scharfglass is local and brought his sympetrum boards to show during the evening. Based on Neal Stephenson’s book The Diamond Age, these badges will synchronize their colors when in the same room together. Kerry built version 2 of the badge for last year’s DEF CON but what is show here is the work-in-progress version 3. And we also got to see a bit of behind-the-scenes of building blinky LED badges as Kerry brought a development tool featuring 3D-printed jig holding pogo pins to interface with his v3 board.
We invited Hackaday Prize participants to bring their entries, and Michael Graham is among those who answered the call. His Mug-O-Matic is a demonstration piece for his linear actuator module, one of twenty winners of our Robotics Module challenge! Sadly we didn’t get a chance to see Mug-O-Matic in action as Michael’s beverage came in a small plastic cup instead of a suitable mug. But the cup was enough to fuel the main purpose of the night: chatting about hacks and hacking.


The further back you go into the room, the more crowded and louder it got, but the effort will be rewarded with projects plugged into power outlets on the back wall. A spectacular example was the Volumetric POV Display by Jamal Davis. His project has everything — custom LED circuit boards, wires to power them, motor to spin them, micro controller to orchestrate everything, all housed inside a 3D-printed enclosure.
It was impressive enough to look at even before it was turned on. Once it started spinning, the light show stole all the attention.
The above are just a sample of creations lighting up tables at this year’s Hackaday x Tindie BAMF meetup. The projects get more amazing every year. Join us next year to see what wonderful creations show up!