Sometimes, mechanical parts can be supremely expensive, or totally unavailable. In those cases, there’s just one option — make it yourself. It was this very situation in which I found myself. My electric scooter had been ever so slightly bested by a faster competitor, and I needed redemption. A gearing change would do the trick, but alas, the chain sprocket I needed simply did not exist from the usual online classifieds.
Thus, I grabbed the only tools I had, busied myself with my task. This is a build that should be replicable by anyone comfortable using a printer, power drill, and rotary tool. Let’s get to work!
Getting Started
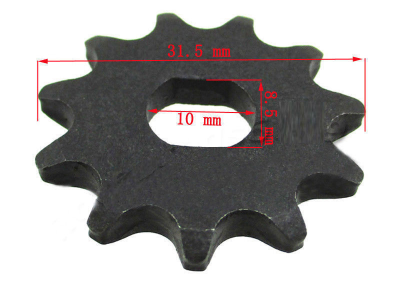
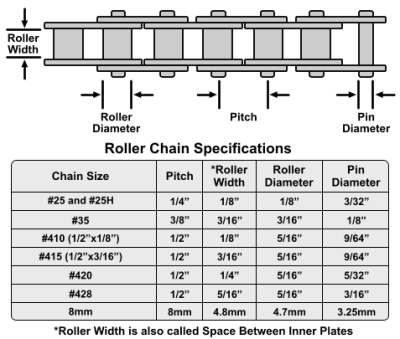
Making a sprocket is easy — print a template, stick it to a metal blank, and cut it out. There’s some post-processing required, but the fundamental concept is little different from any basic woodworking or craft project.
Making a template is easy, using a free piece of software called Sprocketeer 2.0. Sprockets actually have remarkably complex geometry, designed to make chain drives that run as quietly, smoothly, and efficiently as possible. All you need is the pitch and roller diameter of your chosen chain, and the number of teeth of your desired sprocket, and Sprocketeer will generate the outline.
I was producing a sprocket for T8F chain, and a Google search netted me the relevant dimensions: 8 mm pitch with a roller diameter of 4.7 mm. I also knew I wanted a 19-tooth sprocket, in order to hit my desired top speed. Plugging these numbers into the software then netted me a DXF file, which I was able to import into Inkscape. From there, I added on the geometry for the ovaloid mount which I was able to grab from eBay listings images for similar sprockets. With that done, it was a simple matter of printing out the template on a sheet of A4 paper. I was careful to check that the final result was accurately sized before committing to the next stage of the build, something simple to do as I know the exact dimensions of the ovaloid.
That’s Pretty Metal
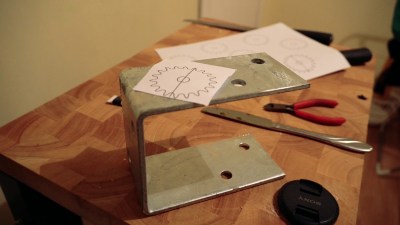
Next, you’ll need some metal with which to craft your sprocket. Mild steel is a typical choice, with the toughness required for the job while still being cheap and easy to machine. They’re also more likely to wear-in nicely versus harder steels, something which we’ll revisit later.
My choices were limited given I was only looking to make a small sprocket of around 60mm diameter, and 4mm thick. The closest I could find was 75 x 50 mm, in a 3 meter length, at an exorbitant cost. Being resourceful, I found a galvanized post support for just $10 that I could cut up, albeit it was 5mm thick. This would require some further work, but would do the job just fine.
Cut It Up!
Once you’ve got your paper template, it’s a simple matter of roughing up your metal and attaching it to the surface with super glue. Then you’re ready to start cutting. A good approach is to first rough out the general shape of the sprocket by making long straight cuts with an angle grinder. Once you have a roughly octagonal blank, proceed to start cutting away at the gaps in between the teeth. At this stage, it’s important to be conservative and not cut over the lines of the template. I used the grinder to just take small cuts on either side of the template, resulting in very rough and oversized teeth — refinement comes later.
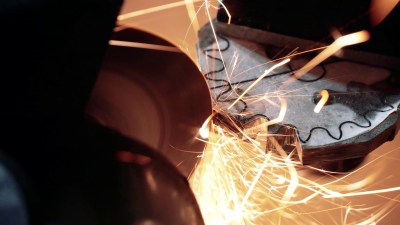
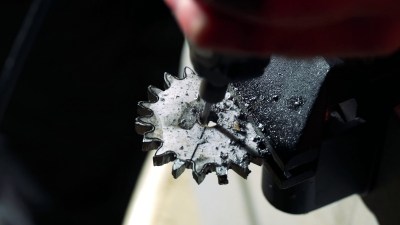
This is a good time to rough-cut the mounting hole in the center of the sprocket. Depending on how your sprocket mounts, you may need to use different techniques. A power drill is usually a good way to get started. If you’re going for an ovaloid or D-shaped mounting hole, a rotary tool like a Dremel is a great way to machine it out. I started with a 561 Multipurpose Cutting Bit, however as we’re cutting steel, a tungsten carbide bit like the 9903 cutter is a much better choice.
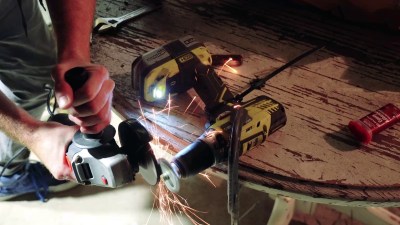
Before proceeding further with cutting the teeth, I needed to thin down the sprocket blank. T8F has a roller width of 4.8mm, but most sprockets are just 4mm thick, tapering down to about 2.5mm to make them mesh smoothly with the chain. My blank was 5mm thick, which simply wouldn’t do. This is a job for a lathe. Thankfully, it’s easy to make your own lathe with just a power drill and a G-clamp.
Start by installing a nut and bolt through the mounting hole of your sprocket. Then, use a G-clamp to mount your drill to a dining table workbench and fit the sprocket in the chuck. Once mounted securely, a ziptie can be used on the drill’s trigger to keep it running at maximum speed. This leaves you with two free hands with which to operate the angle grinder. Using a grinding disc, delicately grind away at the surface of the sprocket blank while it rotates in the drill.
Despite the jerry-rigged nature of this setup, it allowed me to easily machine down the sprocket to an appropriate width. I was even able to neatly taper the teeth, which helps the chain run better when suffering minor misalignments.
Finishing The Teeth
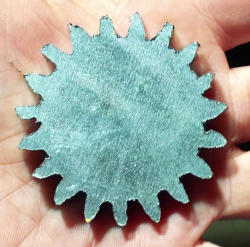
At this point, you should have a neatly machined sprocket blank with ugly, chunky teeth. The angle grinder is simply too crude a tool to finish cutting the teeth, though my father before me has achieved the task. Instead, use a rotary tool. I have had success using the 953 grinding stone, however the 9903 cutting bit is a far better choice for cutting steel. This allows one to slowly and carefully machine away at the teeth without risk of accidentally cutting one off entirely.
After all this cutting, you’ll likely find your template is no longer affixed to the sprocket. Carefully grind away at the teeth, using an existing sprocket as a visual reference. Work around the sprocket, machining away little by little while repeatedly wrapping the chain around to check the fit. The chain needs to be able to smoothly mesh with the sprocket, and slide on and off easily to avoid binding or derailment. The trick to achieving this is to make a nice rounded pocket for the rollers to sit in, while making sure the teeth have a smooth profile that won’t catch on the chain as it slides on and off. Comparing to an existing sprocket is a great way to get an idea of the geometry you’re going for.
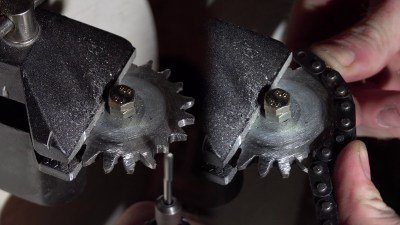
During this process, I had to take a lot of metal off the sprocket, and the teeth ended up looking pretty janky. Some of them looked remarkably thin and pointy, and others looked like tiny little nubs. It’s a long way from the ideal chain profiles you’ve seen in the textbooks. However, my experience with other builds of this type had me confident that this would work. After an hour or so, I had my sprocket meshing well with the test chain, and set about fitting it to the scooter.
The Proof Is In The Scooting
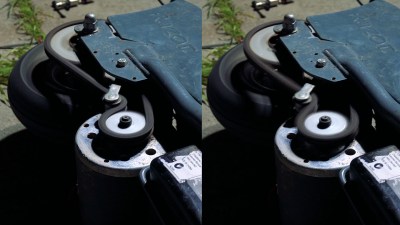
If you’ve gotten this far, congratulations! You’ve got a DIY sprocket that may look a little funky, but hopefully meshes well and is ready for testing. Get it mounted up, lubricate judiciously, and enjoy!
I was eager to test my creation, and set to work. Getting the sprocket mounted involved a little mucking about, as is usual. The mounting hole didn’t fit at first, so I used an existing sprocket as a template and machined things out a little more again using the tungsten carbide bit. The chain also required extension to fit the larger pinion.
Before going for a ride, I propped the scooter up and gave the driveline a test. I revved the motor, and the chain drove the rear wheel as expected. Thankfully, the chain didn’t derail or jam on the new sprocket, so things were looking good. There was some minor skipping, but nothing I was too worried about. With a 500 W motor, an 80kg rider, and with the new sprocket made of mild steel, I was fairly confident that it would wear in nicely and become smoother over time. As the chain was in poor shape, I gave it a liberal lashing of lubricant, with the only thing to hand — 75W differential oil. It stinks like heck, but it’s an excellent chain lube.
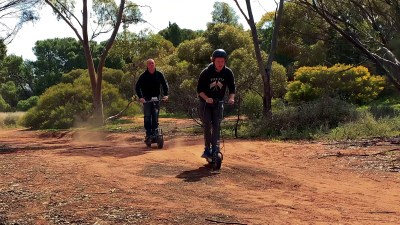
To my absolute joy, the new sprocket performs like a dream. Whether accelerating under heavy load or flying along at top speed, the chain only got smoother as I rode on. After doing a few laps of the block, I freshly charged my batteries and set out on a top speed run. Tearing down a nice straight road, I managed to hit 41 km/h, just over my goal. Suffice to say, I was ecstatic.
I’ve now put many more miles on the sprocket, and it continues to hold up well. While it’s likely not as hardy as a commercially manufactured part, it’s a great substitute for that which was not available. My scooter is now suitably quick, and thanks to a little DIY, I was able to beat all my friends in a straight line drag. I’m calling that a successful build!
No comments:
Post a Comment