I admit: a few years of prototyping without easy machine shop access really whets my tastebuds for turning metal chips. But all that time spent away from proper machine tools has also pushed me to re-imagine part catalogs, something I see almost every day. Without any precision metalworking tools handy, stock mechanical parts have become my supplement for complexity. And so a former dogma to machine-everything-thyself has been transformed into a hunt for that already-made-part-that-does-it-for-you.
But with part catalogs featuring tens of thousands of purpose-built parts, I started reimagining some of them for other misdeeds. And after a few years spent reinventing use cases for some of these parts, I’m about ready to tell you how to misuse them properly. So today I’d like to show you some of my favorite mechanical part B-sides, so to speak. These are ordinary parts in unorthodox places–something you surely won’t find in the datasheet! Now let’s have a look.
From Steel Balls and Pins to Kinematic Couplings
To warm things up, let’s start with kinematic couplings. Kinematic couplings are a mechanical design pattern that, when applied to two components, allows those components to connect and disconnect with extreme repeatability. This property comes from following the method of exact-constraint. By design, the two components are connected together with exactly one constraint per degree of freedom, no more, no less. The result is that, when connected together, coupled parts neither bind nor wiggle; they fit together one and only one way.
Kinematic couplings are often used in optical instrumentation setups where mirrors and lenses need to be finely adjusted without, of course, binding or wiggling. Typically these couplings are manufactured from extremely dense materials like hardened steel such that the coupling’s points of contact don’t deform. That may be all well and good for Thorlabs, but we too can make some decent Maxwell couplings from a mishmash of stock and 3D printed parts.
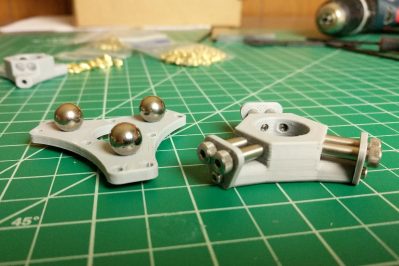
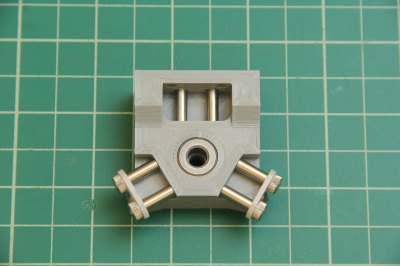
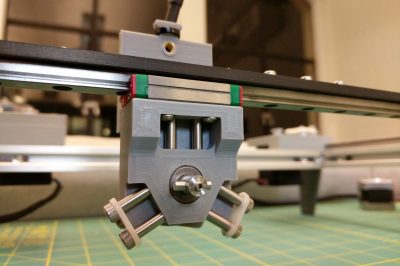
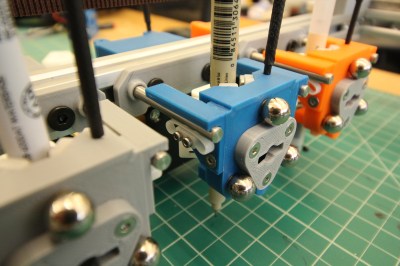
In this setup, the six points of contact in the coupling are made from hard steel parts like their expensive counterparts, but everything else is 3D printed. Since the points of high stress in this design are covered by dense components, the result is both fairly repeatable while being mostly-3D-printed. In fact, in testing the coupling above, I’ve observed a consistent repeatability just under 25 microns. Sure, that may be more than the sub-micron repeatability of some high end couplings, but for many applications it’s fantastic.
I’ve experimented with setups like the one above with a mix of press-fit dowel pins or shoulder screws combined with threaded steel balls. The dowel pins and shoulder screws are quick finds on McMaster-Carr or Aliexpress, but the threaded balls are actually 3D printer replacement parts from a Kossel Delta 3D printer. It goes to say that our palate of stock parts need not be limited to component catalogs exclusively but can extend into the ecosystem of RC, 3D Printer, and other hobbyist replacement parts now commoditized by the consumer goods they go into.
Battery Clips Recast for Fixturing
Now let’s redirect our precision locating adventures out of the optics lab and into the wet lab where we find ourselves working with 96-well plates. In an automated setup, these plates will be fixed into a machine deck where an overhead robot will perform liquid transfers on them. Here, plates need to be held tight enough so they don’t move with machine vibration–but not too tight–or they’ll risk spilling when scientists arrive on scene to collect them.
A gentle preload to hold these well plates in a fixed position would be ideal here. Some sort of leaf spring would be nice, but custom leaf springs are expensive. So let’s ask: what’s another canonical part offering gentle preload that comes in all shape and sizes? Battery clips of course!
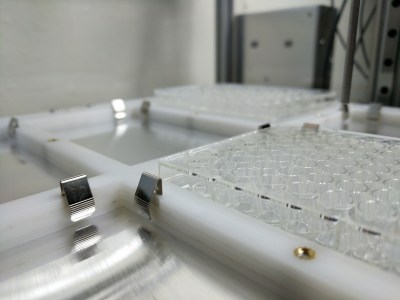
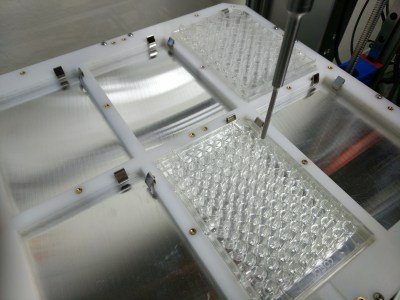
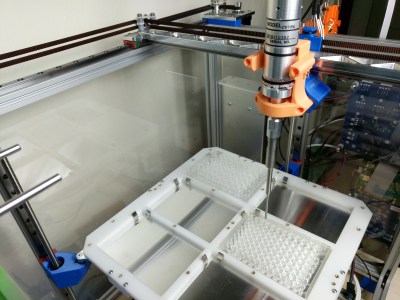
Here I opted for Keystone Electronics’ 5205 Battery Contact Spring (Digikey) intended for molded plastic. My setup resulted in press-fitting them into three stacked layers of laser cut Delrin without any batteries, but shh–the contacts will never know the difference! Since battery contacts are designed to be compressed for long periods of time without fatiguing, the contacts shouldn’t weaken from plates in the fixture overnight. (No word on how many cycles they’re rated for, but for a budget prototype these will do just fine.)
Mini Spring Anchors on a Budget
Now let’s transition to working with extension springs. These springs often arrive with loops on each end to make them easier to attach into their target application. But when it comes to hooking them into 3D printed or laser-cut plastic parts, attaching springs to small integrated plastic features risks them tearing out of the part.
One solution is a stock part called a spring hook or spring anchor. While large spring anchors tend to be prolific, small ones aren’t. Alas, in my original hunt for spring anchors, I could only turn up one Misumi part at the M3 scale I was looking for. And at $5 apiece, they’re exorbitantly more expensive than other stock parts in my fastener bucket. As for simply opting for a screw in this case, it turns out that they make inconvenient spring anchors for two reasons: (1) the head gets in the way of installing the spring and (2) they only work well if the extension spring can be installed perpendicular to the screw. Surely, I thought, there must be a cheaper solution in this pile of part catalogs.
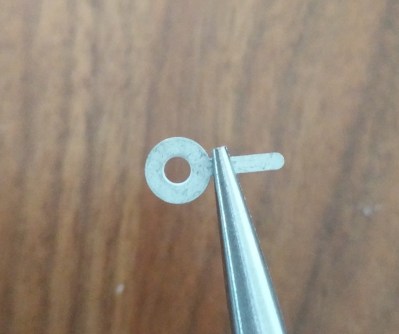
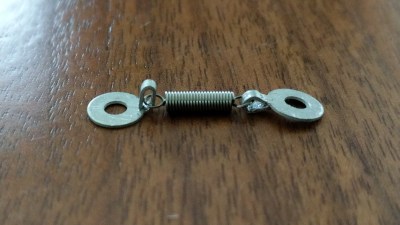
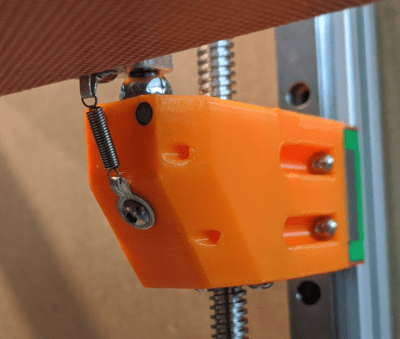
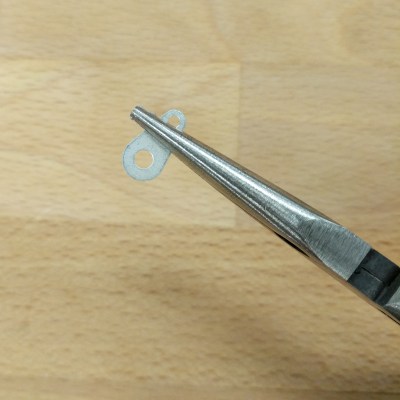
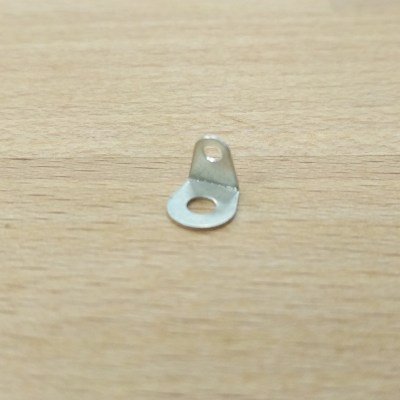
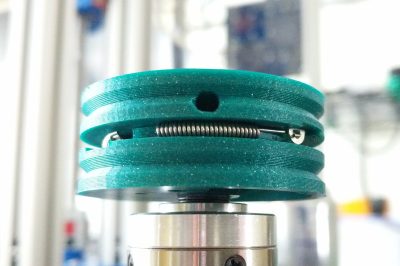
And there was! The answer arrived in the form of solder terminal lugs. These are normally intended to be soldered into a wire at one end and screwed into an electrical terminal at the other. And at about 20 cents apiece, they’re also quite cheap. Best of all, since they’re made from brass, they can be formed with pliers into a shape that’s convenient for retaining the spring at a particular orientation. I’ve used both Keystone Electronics’ 7328 (Digikey) and 4000 (Digikey) parts to hole small extension springs in compact odd configurations each of which was gently “pliered” into a convenient orientation first.
Vented Screws reimagined as Cable Tensioners
These next parts hearken back to my 3 part mini-series building up two-stage animatronic tentacle mechanisms. These systems are driven with a pair of hand controllers that tug on a set of mechanical control cables. Just like a bicycle, having these cables adjustable for proper tension is key to getting them to work smoothly without any perceivable “slop” or backlash. Bicycles rely on a screw based mechanism that lets the user fine tune the tension by effectively changing the length of the cable housing. Could I use a stock part to do the same thing?
Yes! It turns out I’d been ogling McMaster-Carr’s vented screws category for a couple years hoping I’d someday have an excuse to buy them, and the time had finally arrived. Vented screws are essentially screws with a small hole drilled down the center. Were I some process engineer specializing in pressure vessels, I’d probably tell you how these screws, combined with an o-ring, form a useful part of a servoed pressure control system. But I can’t. What I can tell you is that threading the mechanical control cable through these vented screws creates an exceptional cable tension adjustment point.
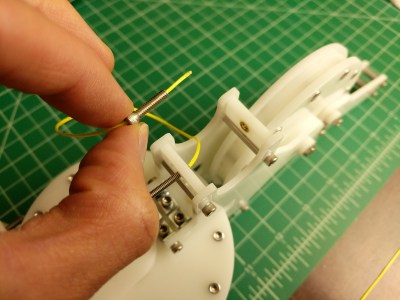
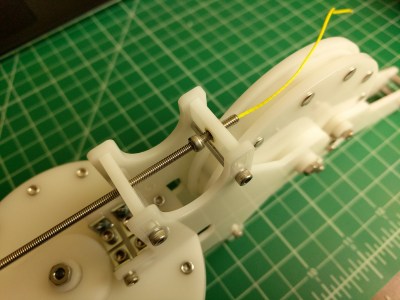
By installing one vented screw per cable into the into the laser-cut controller, the entire system can be fine tuned for a high-fidelity puppeteering performance as compelling as the good ol’ 1979 Alien chest-burster scene.
The Standoff Sandwich
Standoffs are metal posts threaded at both ends. They might be the electronic engineer’s go-to for mounting circuit boards, but I’d claim they’re a great way to mounting many mostly-flat components–not just circuit boards–in a rapid prototyping or hobbyist use case. I call this technique the standoff sandwich, and I’ve mentioned it once before. Here standoffs combine with laser-cut elements to build up a 3D structure. Since they’re available in a range of lengths, we sidestep the need to machine parts to length by simply buying the part at the correct length. We need not limit ourselves to one layer either. Double and triple-decker standoff sandwiches are all fair game too. And at about 50 cents apiece, the overall costs for a significant portion of your structure can be fairly cheap too.
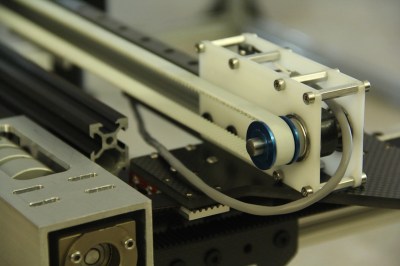
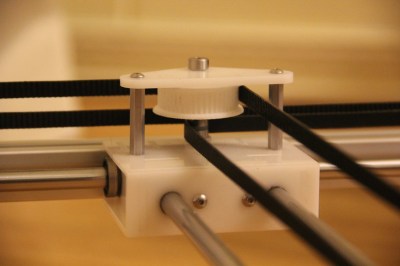
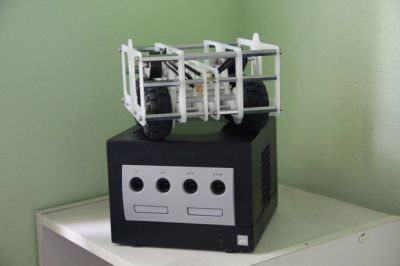
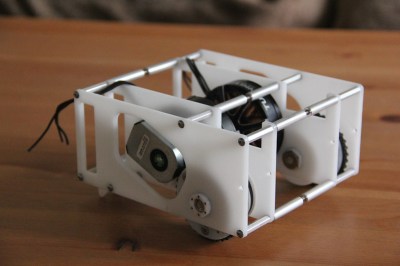
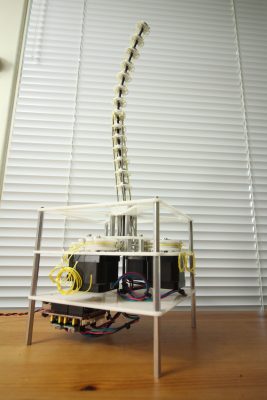
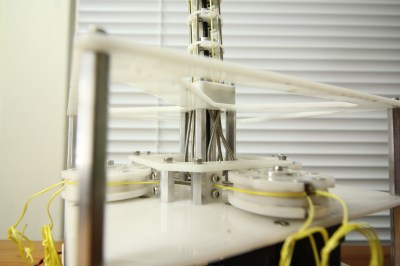
These days, I find them useful for small scale robotics applications when mixed with 3D printed or laser cut parts.
A Vocabulary of Parts
It’s been two years since I tore down my garage “machine shop” and took the leap back to school for one last mission. With my best tools in the deep sleep of storage, I thought I’d be giving up feeding my part-hungry soul with a steady stream of machining projects.
But something else happened. Far away from the tools, I found part catalogs. These field guides to the “pickings” of “Part Land” became my saving grace, a new way to design widgets–without actually machining anything! And with some creative use-case reimagining, I discovered that the capabilities of this part vocabulary go far beyond what the books say. With today’s examples, I hope you start to see that too. So the next time you need a little machine shop “glue logic,” I hope you challenge yourself to go beyond what you can make and include the span of what you can find too.
No comments:
Post a Comment